Aluminum alloy two-step anodizing process
A secondary anodic oxidation, anodic oxidation technology, applied in the direction of electrolytic coating, surface reaction electrolytic coating, coating, etc., can solve the problems of reducing the anti-corrosion performance of anodized film, reducing the anti-corrosion performance of aluminum alloy, local current concentration, etc. , to achieve the effect of low production cost, simple and easy operation, and protection of aluminum alloy
- Summary
- Abstract
- Description
- Claims
- Application Information
AI Technical Summary
Problems solved by technology
Method used
Image
Examples
Embodiment 1
[0023] (1) Surface pretreatment of aluminum alloy styles
[0024] Grinding and cleaning: Use water sandpaper to grind from 400# to 1200# in sequence, then use ultrasonic cleaning in ethanol solution for 5 minutes, take it out, rinse it with distilled water, and dry it with cold air;
[0025] Chemical degreasing: degreasing solution: sodium hydroxide: 10g / L, coconut oil diethanolamine: 2g / L, nonylphenol polyoxyethylene ether: 0.5g / L. Use a magnetic stirrer in the degreasing solution, the speed is 60r / min, the reaction time is 2min, take it out, wash it with distilled water, and dry it with cold air;
[0026] Pickling light: pickling solution: nitric acid: 5g / L, sodium nitrate: 10g / L, sodium phytic acid: 3g / L. Use a magnetic stirrer in the pickling solution with a rotating speed of 60r / min and a reaction time of 2min, take it out, rinse it with distilled water, and dry it with cold air.
[0027] (2) The first anodizing
[0028] Use a mixed solution of 30g / L oxalic acid and 20...
Embodiment 2
[0036] (1) Surface pretreatment of aluminum alloy styles
[0037] Grinding and cleaning: Use water sandpaper to grind from 400# to 1200# in sequence, then use ultrasonic cleaning in ethanol solution for 8 minutes, take it out, rinse it with distilled water, and dry it with cold air;
[0038] Chemical degreasing: degreasing solution: sodium hydroxide: 15g / L, coconut oil diethanolamine: 4g / L, nonylphenol polyoxyethylene ether: 2g / L. Use a magnetic stirrer in the degreasing solution, the speed is 60r / min, the reaction time is 2min, take it out, wash it with distilled water, and dry it with cold air;
[0039] Pickling light: pickling solution: nitric acid: 10g / L, sodium nitrate: 7g / L, sodium phytic acid: 1g / L. Use a magnetic stirrer in the pickling solution with a rotating speed of 60r / min and a reaction time of 2min, take it out, rinse it with distilled water, and dry it with cold air.
[0040] (2) The first anodizing
[0041] Use a mixed solution of 40g / L oxalic acid and 15g / ...
Embodiment 3
[0049] (1) Surface pretreatment of aluminum alloy styles
[0050] Grinding and cleaning: Use water sandpaper to grind from 400# to 1200# in sequence, then use ultrasonic cleaning in ethanol solution for 10 minutes, take it out, rinse it with distilled water, and dry it with cold air;
[0051]Chemical degreasing: degreasing solution: sodium hydroxide: 20g / L, coconut oil diethanolamine: 8g / L, nonylphenol polyoxyethylene ether: 5g / L. Use a magnetic stirrer in the degreasing solution, the speed is 60r / min, the reaction time is 2min, take it out, wash it with distilled water, and dry it with cold air;
[0052] Pickling: pickling solution: nitric acid: 20g / L, sodium nitrate: 5g / L, sodium phytic acid: 0.1g / L. Use a magnetic stirrer in the pickling solution with a rotating speed of 60r / min and a reaction time of 2min, take it out, rinse it with distilled water, and dry it with cold air.
[0053] (2) The first anodizing
[0054] Use a mixed solution of 50g / L oxalic acid and 10g / L ci...
PUM
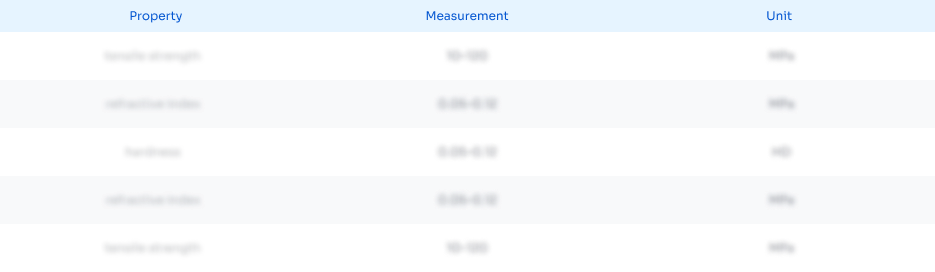
Abstract
Description
Claims
Application Information

- R&D
- Intellectual Property
- Life Sciences
- Materials
- Tech Scout
- Unparalleled Data Quality
- Higher Quality Content
- 60% Fewer Hallucinations
Browse by: Latest US Patents, China's latest patents, Technical Efficacy Thesaurus, Application Domain, Technology Topic, Popular Technical Reports.
© 2025 PatSnap. All rights reserved.Legal|Privacy policy|Modern Slavery Act Transparency Statement|Sitemap|About US| Contact US: help@patsnap.com