Preparation method for preparing graphene oxide anti-corrosion protective film on metal surface
An anti-corrosion, metal surface technology, applied in metal material coating process, coating, etc., can solve the problems of less film deposition times, slow release efficiency and poor wear resistance
- Summary
- Abstract
- Description
- Claims
- Application Information
AI Technical Summary
Problems solved by technology
Method used
Image
Examples
Embodiment 1
[0027] 1) Preparation of Ce-CF conversion film on aluminum alloy surface
[0028] Use sandpaper to polish the 2A12 aluminum alloy test piece to remove impurities and oxide film until a bright surface appears, then rinse it with distilled water, then ultrasonically clean it with acetone, dry it and use it as a blank sample for later use. Hang the processed aluminum alloy bare chip with a clean wire and put it into a beaker filled with 0.5mol / L cerium nitrate solution for 30 minutes for later use. Put the cerium nitrate-treated test piece into an oven preheated to 80 degrees Celsius and bake for 30 minutes to obtain the Ce-CF conversion coating.
[0029] 2) Preparation of LBL-1 self-assembled film on aluminum alloy surface
[0030] Put the aluminum alloy test piece of the surface Ce-CF conversion film prepared above into a beaker containing 4mg / ml PEI and soak for 5 minutes, take it out in a beaker containing distilled water for 2 minutes, then put it into a beaker containing 4...
Embodiment 2
[0041] 1) Preparation of Ce-CF conversion film on aluminum alloy surface
[0042] Use sandpaper to polish the aluminum alloy test piece to remove impurities and oxide film until a bright surface appears, then rinse it with distilled water quickly, then use ethanol to ultrasonically clean it, dry it and use it as a blank sample for later use. Hang the treated aluminum alloy die with a clean wire and put it into a beaker filled with 0.8mol / L cerium nitrate solution and soak for 20 minutes for later use. Put the cerium nitrate-treated test piece into an oven preheated to 60 degrees Celsius and bake for 50 minutes to obtain the Ce-CF conversion coating.
[0043] 2) Preparation of LBL-1 self-assembled film on aluminum alloy surface
[0044] Put the titanium alloy test piece of the surface Ce-CF conversion film prepared above into the beaker containing 6mg / ml PEI and soak for 15 minutes, take it out in the beaker with distilled water for 8 minutes, then put it into the beaker conta...
PUM
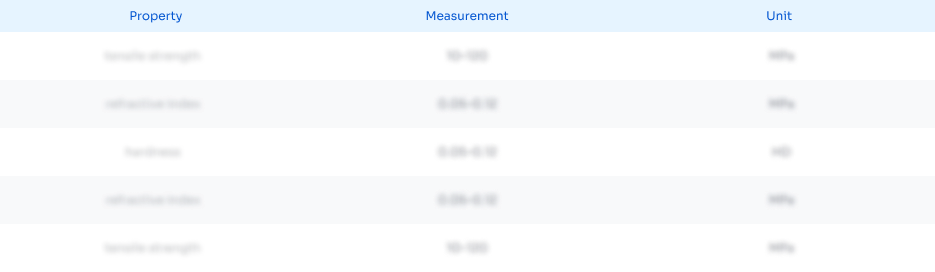
Abstract
Description
Claims
Application Information

- R&D
- Intellectual Property
- Life Sciences
- Materials
- Tech Scout
- Unparalleled Data Quality
- Higher Quality Content
- 60% Fewer Hallucinations
Browse by: Latest US Patents, China's latest patents, Technical Efficacy Thesaurus, Application Domain, Technology Topic, Popular Technical Reports.
© 2025 PatSnap. All rights reserved.Legal|Privacy policy|Modern Slavery Act Transparency Statement|Sitemap|About US| Contact US: help@patsnap.com