Low-ink paper sludge and preparation method thereof
A technology of ink and paper slime, applied in the field of materials, can solve the problems of restricting the application and development of waste newspapers, unsatisfactory ink removal effect, and easy odor of paper slime, etc., to achieve enhanced flotation selectivity, low ink content, and no irregularities porosity effect
- Summary
- Abstract
- Description
- Claims
- Application Information
AI Technical Summary
Problems solved by technology
Method used
Examples
Embodiment 1
[0033] The preparation method comprises the following steps:
[0034] 1) breaking the waste paper to obtain shredded paper sheets in corresponding parts by weight, washing the sediment to remove impurities;
[0035] 2) Then add additives in corresponding parts by weight, add an appropriate amount of water, control the pH value within the acidic range, and carry out micro-fermentation treatment;
[0036] 3) adding thermal initiators of corresponding parts by weight to the material processed through micro-fermentation, and autoclaving and sterilizing;
[0037] 4) Extruding and kneading the material sterilized by high pressure cooking to obtain intermediate fiber slurry;
[0038] 5) adding deinking agent, glycerin and acacia extract of corresponding parts by weight to the intermediate fiber slurry, after stirring evenly, deinking by normal temperature flotation;
[0039] 6) Delamination and fiber separation are performed on the fiber slurry after the flotation deinking treatmen...
Embodiment 2
[0056] The preparation method comprises the following steps:
[0057] 1) breaking the waste paper to obtain shredded paper sheets in corresponding parts by weight, washing the sediment to remove impurities;
[0058] 2) Then add additives in corresponding parts by weight, add an appropriate amount of water, control the pH value within the acidic range, and carry out micro-fermentation treatment;
[0059] 3) adding thermal initiators of corresponding parts by weight to the material processed through micro-fermentation, and autoclaving and sterilizing;
[0060] 4) Extruding and kneading the material sterilized by high pressure cooking to obtain intermediate fiber slurry;
[0061] 5) adding deinking agent, glycerin and acacia extract of corresponding parts by weight to the intermediate fiber slurry, after stirring evenly, deinking by normal temperature flotation;
[0062] 6) carrying out latent elimination and fiber separation of the fiber slurry after the flotation and ink remova...
Embodiment 3
[0079] The preparation method includes the following steps:
[0080] 1) smashing the waste paper to obtain the shredded paper sheet of corresponding parts by weight, washing the sediment to remove impurities;
[0081] 2) then add the additive of the corresponding parts by weight, add an appropriate amount of water, and the pH value is controlled within the acid range to carry out micro-fermentation treatment;
[0082] 3) adding the thermal initiator of corresponding parts by weight to the material subjected to the micro-fermentation treatment, and autoclaving and sterilizing;
[0083] 4) Squeeze and knead the material sterilized by autoclaving to obtain intermediate fiber slurry;
[0084] 5) adding the deinking agent, glycerin and acacia extract of corresponding parts by weight to the intermediate fiber slurry, after stirring evenly, the ink is removed by flotation at room temperature;
[0085] 6) carrying out latent elimination and fiber separation of the fiber slurry after...
PUM
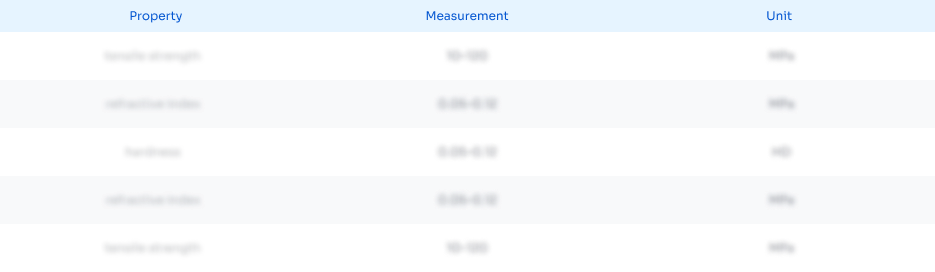
Abstract
Description
Claims
Application Information

- Generate Ideas
- Intellectual Property
- Life Sciences
- Materials
- Tech Scout
- Unparalleled Data Quality
- Higher Quality Content
- 60% Fewer Hallucinations
Browse by: Latest US Patents, China's latest patents, Technical Efficacy Thesaurus, Application Domain, Technology Topic, Popular Technical Reports.
© 2025 PatSnap. All rights reserved.Legal|Privacy policy|Modern Slavery Act Transparency Statement|Sitemap|About US| Contact US: help@patsnap.com