Autocatalytic denitrification process of sintering flue gas based on utilization of windbox flue dust waste heat
A technology of self-catalysis and bellows, applied in gas treatment, chemical instruments and methods, separation methods, etc., can solve the problems of high one-time investment cost of SCR technology, increase of SCR denitrification operation cost, large heat consumption and other problems, and achieve saving of denitrification equipment The effect of investment, denitrification equipment investment reduction, and small footprint
- Summary
- Abstract
- Description
- Claims
- Application Information
AI Technical Summary
Problems solved by technology
Method used
Image
Examples
Embodiment 2
[0046] see figure 2 , no fluidized bed reactor 7 is provided, and the sintering dust is directly sent into the high-temperature flue gas main flue 9 without the fluidized bed reactor 7, and the rest is the same as that of embodiment 1.
Embodiment 3
[0048] see image 3 , the low-temperature flue gas main flue 10 and the fluidized bed reactor 7 are not provided, and the sintering dust in the bellows 5 is all directly sent into the high-temperature flue gas main flue 9, and the rest is the same as in embodiment 1.
PUM
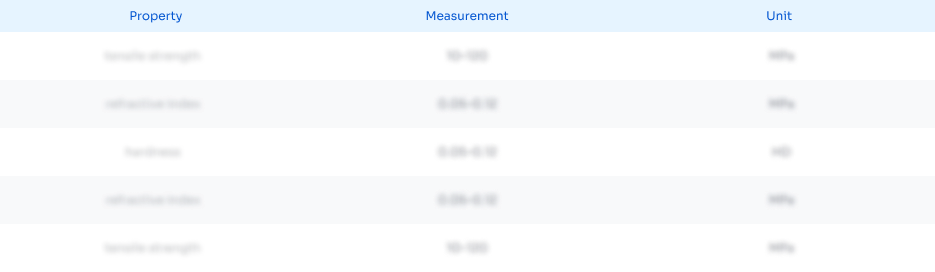
Abstract
Description
Claims
Application Information

- Generate Ideas
- Intellectual Property
- Life Sciences
- Materials
- Tech Scout
- Unparalleled Data Quality
- Higher Quality Content
- 60% Fewer Hallucinations
Browse by: Latest US Patents, China's latest patents, Technical Efficacy Thesaurus, Application Domain, Technology Topic, Popular Technical Reports.
© 2025 PatSnap. All rights reserved.Legal|Privacy policy|Modern Slavery Act Transparency Statement|Sitemap|About US| Contact US: help@patsnap.com