Device and method for forming seamless dual-layer spiral coil pipe
A technology of spiral coil and forming device, which is applied to forming tools, heat exchange equipment, metal processing equipment, etc., can solve the problems of complex manufacturing and difficult modification of welding defects, and achieve the effect of difficult repair, simple structure and defect avoidance.
- Summary
- Abstract
- Description
- Claims
- Application Information
AI Technical Summary
Problems solved by technology
Method used
Image
Examples
Embodiment 1
[0025] Such as Figure 2-4 shown.
[0026] A seamless double-layer spiral coil forming device, which mainly includes a lathe middle carriage 1 capable of moving left and right or forward and backward, a base 2, a roller bracket 3, an angle-adjustable roller 4, an inner pipe mold 5, an outer layer The tube upper die 7 and the outer tube lower die 8, the base 2 are fixed on the middle carriage 1 of the lathe through T-shaped slots, and the bottom of the roller bracket 3 is provided with four waist-shaped installation and fixing holes, which can be fixed on the base 2 by bolts And the circumferential adjustment of the position can be realized; the roller 4 is installed on the roller shaft 12, and the roller shaft 12 is fixed in the elongated slot 13 on the column of the roller bracket 3 by a nut, adjusting the position of the roller shaft can realize the adjustment of the height of the roller Adjustment. When the inner layer spiral coil is processed, the left end of the inner l...
Embodiment 2
[0028] Such as Figure 2-4 as shown
[0029] A seamless double-layer spiral coil forming method, it comprises the following steps:
[0030] First, the original tool holder of the lathe is removed, and the base 2 is fixed on the middle carriage 1 of the lathe through T-slot bolts. The lower part of the roller bracket 3 is designed with 4 waist holes, which can realize its rotation in the vertical direction. Adjust the rotation angle of the roller bracket 3 according to the rising angle of the inner right-handed spiral coil, keep the two consistent, and then tighten it with screws fixed on the base 2. Adjust the height of the roller 4 in the roller bracket 3 so that the straight pipe that penetrates under the roller 4 can be tangent to the upper part of the inner layer pipe mold 5, and then tighten the hexagonal flange nuts at both ends of the central axis of the roller 4. Pass the straight pipe under the roller 4, press the end on the inner pipe mold 5 through the pressing b...
PUM
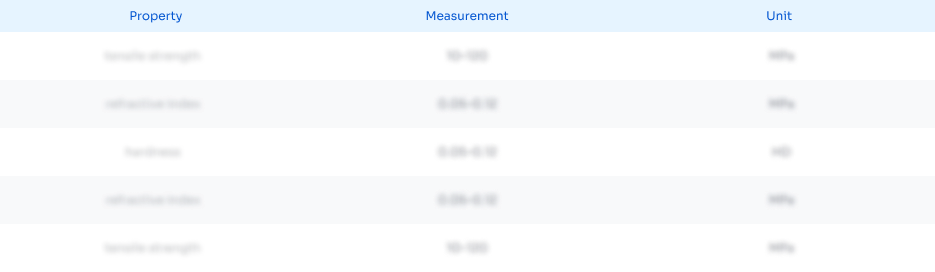
Abstract
Description
Claims
Application Information

- R&D Engineer
- R&D Manager
- IP Professional
- Industry Leading Data Capabilities
- Powerful AI technology
- Patent DNA Extraction
Browse by: Latest US Patents, China's latest patents, Technical Efficacy Thesaurus, Application Domain, Technology Topic, Popular Technical Reports.
© 2024 PatSnap. All rights reserved.Legal|Privacy policy|Modern Slavery Act Transparency Statement|Sitemap|About US| Contact US: help@patsnap.com