A combined recovery method of dressing and metallurgy in zinc oxide ore
A technology of combined beneficiation and smelting and recovery method is applied in the field of combined beneficiation and smelting recovery of zinc in zinc oxide ore, which can solve the problems of increased production cost, inability to remove fine mud, large leaching reagents, etc., and achieve cost saving and recycling value. The effect of highlighting and reducing adverse effects
- Summary
- Abstract
- Description
- Claims
- Application Information
AI Technical Summary
Problems solved by technology
Method used
Examples
Embodiment 1
[0017] (1) Grinding: A zinc oxide mine in Yunnan, the zinc grade in the raw ore is 5.32%, the oxidation rate is 93%, and the mud content is 20%; the ore is mostly beige, gray, a few reddish brown, lead gray, and the gangue minerals are mainly Mainly quartz; the grinding concentration is 50%, the content of grinding fineness less than 0.074mm is 90%, and the obtained pulp mass percentage concentration is 35%;
[0018] (2) Slime reverse flotation: Add 10g / t kerosene and 20g / t No. 2 oil to the pulp in step (1), and obtain slime and tailings pulp with a mass percentage concentration of 33% after reverse flotation;
[0019] (3) Zinc concentrate flotation: Add 4Kg / t sodium sulfide, 300g / t propyl salicylaldoxime and 150g / t alkyl propyl ether amine in turn to the tailings slurry in step (2), after two times of roughing, The flotation concentrate and flotation tailings are obtained after two beneficiation and one sweeping; among them, the recovery rate of flotation operation is 85.60%;...
Embodiment 2
[0022] (1) Grinding: A zinc oxide mine in Guangxi, the zinc grade in the ore is 4.62%, the oxidation rate is 84%, the mud content is 30%, and the gangue minerals are mainly carbonates; the grinding concentration is 55%, and the grinding fineness is less than The content of 0.074mm is 95%, and the mass percentage concentration of the obtained pulp is 37%;
[0023] (2) Slime reverse flotation: Add 30g / t kerosene and 15g / t No. 2 oil to the pulp in step (1), and obtain slime and tailings pulp with a mass percentage concentration of 34% after reverse flotation;
[0024] (3) Zinc concentrate flotation: Add 3Kg / t sodium sulfide, 200g / t propyl salicylaldoxime and 200g / t alkyl propyl ether amine in turn to the tailings slurry in step (2), after two times of roughing, The flotation concentrate and flotation tailings are obtained after two beneficiation and one sweeping; among them, the recovery rate of flotation operation is 87%;
[0025] (4) Metal zinc leaching: Combine the ore slime ...
Embodiment 3
[0027] (1) Grinding: A zinc oxide mine in Guizhou, the zinc grade in the raw ore is 6.12%, the oxidation rate is 90%, the mud content is 40%, and the gangue minerals are mainly silicates; the grinding concentration is 55%, and the grinding fineness The content of less than 0.074mm is 90%, and the mass percentage concentration of the obtained pulp is 30%;
[0028] (2) Slime reverse flotation: Add 50g / t kerosene and 5g / t No. 2 oil to the pulp in step (1), and obtain slime and tailings pulp with a mass percentage concentration of 30% through reverse flotation;
[0029] (3) Zinc concentrate flotation: Add 6Kg / t sodium sulfide, 400g / t propyl salicylaldoxime and 100g / t alkyl propyl ether amine to the tailings slurry in step (2) successively, after rough separation and selection , Obtain flotation concentrate and flotation tailings after sweeping; among them, the recovery rate of flotation operation is 88.36%;
[0030] (4) Metal zinc leaching: combine the ore slime in step (2) with ...
PUM
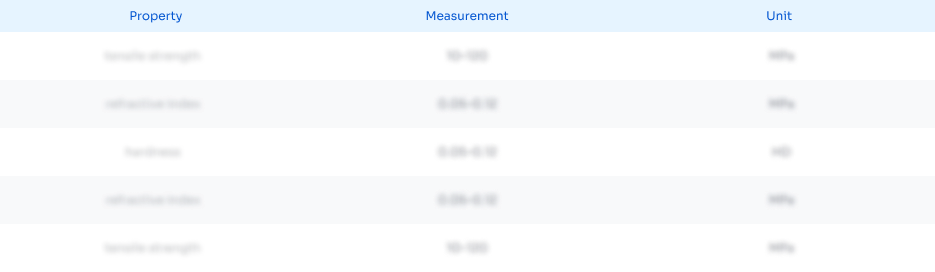
Abstract
Description
Claims
Application Information

- R&D
- Intellectual Property
- Life Sciences
- Materials
- Tech Scout
- Unparalleled Data Quality
- Higher Quality Content
- 60% Fewer Hallucinations
Browse by: Latest US Patents, China's latest patents, Technical Efficacy Thesaurus, Application Domain, Technology Topic, Popular Technical Reports.
© 2025 PatSnap. All rights reserved.Legal|Privacy policy|Modern Slavery Act Transparency Statement|Sitemap|About US| Contact US: help@patsnap.com