A method of using biomass as a bonding carrier to prepare high-strength iron-containing agglomerates and gas-iron cogeneration
A biomass and high-strength technology, applied in the field of ironmaking, can solve the problems of affecting pellet reaction and reduction process, cracking incomplete tar, waste of biomass energy, etc., so as to reduce tar content, strengthen ion deviation effect, and promote The effect of decomposition
- Summary
- Abstract
- Description
- Claims
- Application Information
AI Technical Summary
Problems solved by technology
Method used
Image
Examples
Embodiment 1
[0046] In the process of previous research, the application has made a series of breakthroughs, and has improved the gasification yield and the quality of direct reduced iron, with significant progress, and applied for an invention patent (2017101469513-a biomass gasification and direct reduction The iron co-production method and additives used, the application date is: 2016-03-13). In the process of continuing research, the applicant further found that when using biomass iron-containing agglomerates to produce combustible gas and direct reduced iron, the strength of the produced iron-containing agglomerates is relatively poor, and it is easy to cause the iron-containing agglomerates to be crushed. Then affect the reduction process of iron-containing agglomerates; in addition, the binder will also affect the iron taste and gas yield of direct reduced iron. In order to further improve the quality of direct reduced iron, the applicant has carried out further in-depth research and...
Embodiment 2
[0080] The basic content of the present embodiment is the same as that of Example 1, except that the additive is composed of sodium carbonate, laterite nickel ore, dolomite, plant ash and chromium slag; the mass percent of each component is: sodium carbonate: 15% , Laterite nickel ore: 30%, dolomite: 30%, plant ash: 15%, chromium slag: 10%. Described chromium slag chemical composition mass percent is as follows: SiO 2 : 28%, Al 2 o 3 : 8%, CaO: 30%, MgO: 15%, Fe 2 o 3 : 10%, Cr 2 o 6 : 0.8% and Na 2 Cr 2 o 7 : 1%, the rest are impurities. The metallization rate of direct reduced iron, biomass gasification yield and tar yield were detected after the reaction. The experimental results are recorded in Table 1. On the one hand, the chromium slag can effectively reduce the chromium slag under the high reducing condition of biomass gasification to generate low-priced chromium oxides. The combination of chromium oxides with iron oxides and calcium-magnesium compounds in th...
Embodiment 3
[0083] The basic content of this embodiment is the same as that of Example 1, except that the iron ore concentrate is made up of Hayangdi, Tubalang powder, Canadian fine powder, Kazakh mixed powder and Jinbuba powder, and the composition of the ore is as shown in Table 2 Shown, the mass percentages of various mineral powders are: Hayangdi: 10%, Tubalang powder: 20%, Canadian refined powder: 40%, Kazakhstan powder: 15%, Jinbuba powder: 15%. The metallization rate of direct reduced iron, biomass gasification yield, and tar yield were detected after the reaction. The experimental results are recorded in Table 1.
[0084] Table 2 Mineral powder composition (wt / %)
[0085]
[0086] The metallization rate of direct reduced iron is further improved. Through repeated discussions, the inventor believes that this process may be due to the fact that the crystal water in the iron ore powder is heated and decomposed during the heat preservation process at 900°C, and produces more These...
PUM
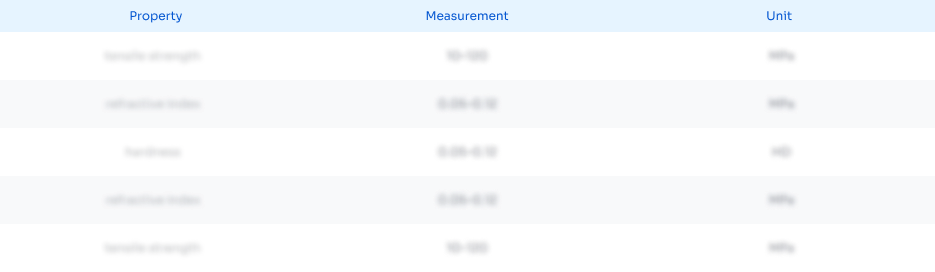
Abstract
Description
Claims
Application Information

- R&D
- Intellectual Property
- Life Sciences
- Materials
- Tech Scout
- Unparalleled Data Quality
- Higher Quality Content
- 60% Fewer Hallucinations
Browse by: Latest US Patents, China's latest patents, Technical Efficacy Thesaurus, Application Domain, Technology Topic, Popular Technical Reports.
© 2025 PatSnap. All rights reserved.Legal|Privacy policy|Modern Slavery Act Transparency Statement|Sitemap|About US| Contact US: help@patsnap.com