Battery connector for solving poor welding, and manufacturing method thereof
A technology of battery connector and manufacturing method, which is applied in the direction of electrical connection of printed components, connection, fixed connection, etc., can solve problems such as board scrapping, copper skin falling, and copper foil heating time for a long time, so as to reduce maintenance costs and strengthen The output of good products and the effect of solving poor welding problems
- Summary
- Abstract
- Description
- Claims
- Application Information
AI Technical Summary
Problems solved by technology
Method used
Image
Examples
Embodiment 1
[0027] Embodiment one: if image 3 As shown, there is one line-shaped copper foil, and the width of the line-shaped copper foil 3 is less than half of the diameter of the pin socket. The line-shaped copper foil absorbs less heat, reduces the heat dissipation rate, and provides sufficient run-off time for soldering, so the pins are soldered firmly and avoid the occurrence of poor soldering.
Embodiment 2
[0028] Embodiment two: if Figure 4 As shown, the line-shaped copper foil includes several strips. And the width of each line-shaped copper foil 3 is less than half of the diameter of the pin socket. The line-shaped copper foil absorbs less heat, reduces the heat dissipation rate, and provides sufficient run-off time for soldering, so the pins are soldered firmly and avoid the occurrence of poor soldering.
[0029] A manufacturing method for solving poorly welded battery connectors, comprising the following steps:
[0030] Step S1: Drill through holes / blind holes on PCB1, and some of the through holes are used as pin jacks. In order to ensure the effect of copper sinking, the drilled through holes / blind holes are ground, swollen and decontaminated to prevent burrs, air bubbles and residues in the through holes / blind holes. The burr in the hole is removed by grinding the hole. After swelling treatment, the air bubbles are removed, and at the same time, the inner wall of the...
PUM
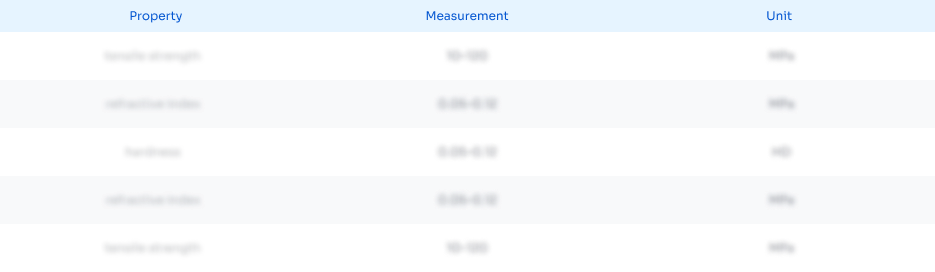
Abstract
Description
Claims
Application Information

- R&D
- Intellectual Property
- Life Sciences
- Materials
- Tech Scout
- Unparalleled Data Quality
- Higher Quality Content
- 60% Fewer Hallucinations
Browse by: Latest US Patents, China's latest patents, Technical Efficacy Thesaurus, Application Domain, Technology Topic, Popular Technical Reports.
© 2025 PatSnap. All rights reserved.Legal|Privacy policy|Modern Slavery Act Transparency Statement|Sitemap|About US| Contact US: help@patsnap.com