Synchronous floating core pulling mechanism for large-angle oblique pulling core and guide block on cavity side of injection mold
A technology of injection mold and core-pulling mechanism, which is applied in the field of large-angle oblique core-pulling on the side of the injection mold cavity, and the field of synchronous floating core-pulling mechanism of the guide block, which can solve the problems of reducing production efficiency, increasing the volume of the mold, and increasing the tonnage of the injection molding machine, etc.
- Summary
- Abstract
- Description
- Claims
- Application Information
AI Technical Summary
Problems solved by technology
Method used
Image
Examples
Embodiment Construction
[0012] The invention relates to a large-angle oblique core-pulling mechanism on the cavity side of an injection mold, and a synchronous floating core-pulling mechanism of a guide block, such as figure 1 — Figure 5 As shown, it includes a cavity 1 and a core 2. There is an injection-molded plastic part 3 between the cavity and the core, and a chute 4 inclined upward at a large angle is formed on the plastic part. A guide block 5, a guide pull hook 6 and a guide post fixing block 7 are arranged under the cavity 1, and a distance groove 8 and a guide hole 9 are arranged in the guide block, and a distance pull nail 10 is arranged in the distance groove, and the guide block is pulled by a distance. The nail is connected with the mold cavity 1, and an oblique core pull 11 is set in the guide hole. One end of the oblique core pull is matched with the chute 4 of the plastic part 3, and the other end of the oblique core pull is formed with an oblique chute 12. On the guide hook 6 An ...
PUM
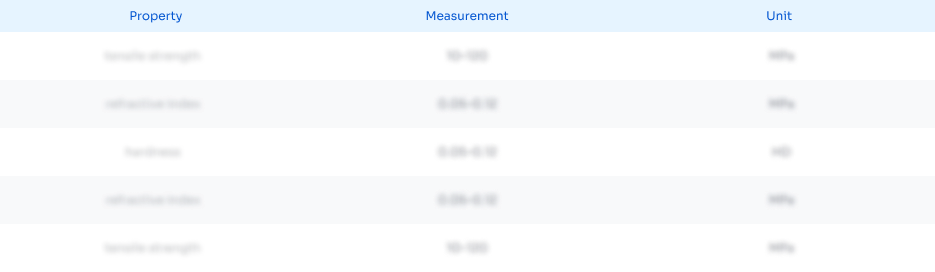
Abstract
Description
Claims
Application Information

- R&D Engineer
- R&D Manager
- IP Professional
- Industry Leading Data Capabilities
- Powerful AI technology
- Patent DNA Extraction
Browse by: Latest US Patents, China's latest patents, Technical Efficacy Thesaurus, Application Domain, Technology Topic, Popular Technical Reports.
© 2024 PatSnap. All rights reserved.Legal|Privacy policy|Modern Slavery Act Transparency Statement|Sitemap|About US| Contact US: help@patsnap.com