Wire frame pole and integrally assembled wire frame pole axial force testing method
A grid rod and assembled technology, which is applied to truss structures, force/torque/work measuring instruments, measuring devices, etc., can solve the problems of large workload, complex force transmission mode, huge workload, etc. Force, huge economic benefits, the effect of simplifying the measurement process
- Summary
- Abstract
- Description
- Claims
- Application Information
AI Technical Summary
Problems solved by technology
Method used
Image
Examples
Embodiment Construction
[0021] The specific embodiments of the present invention will be described in detail below in conjunction with the accompanying drawings.
[0022] A grid rod, such as figure 1 As shown, it includes three structural units, which are the first grid rod round steel pipe 1, the second grid rod round steel pipe 2 and the axial force sensor 3. The three structural units form a whole that participates in the force;
[0023] One end of the first grid rod round steel pipe 1 is connected to one end of the axial force sensor 3 through a high-strength bolt 4, and the other end of the axial force sensor 3 is connected to one end of the second grid rod round steel pipe 2. The data acquisition device connection port 5 of the axial force sensor 3 is connected to the input end of the data acquisition device.
[0024] In this embodiment, the axial force sensor 3 adopts an S-shaped column type axial force sensor, such as figure 2 and image 3 shown.
[0025] The S-column axial force sensor ...
PUM
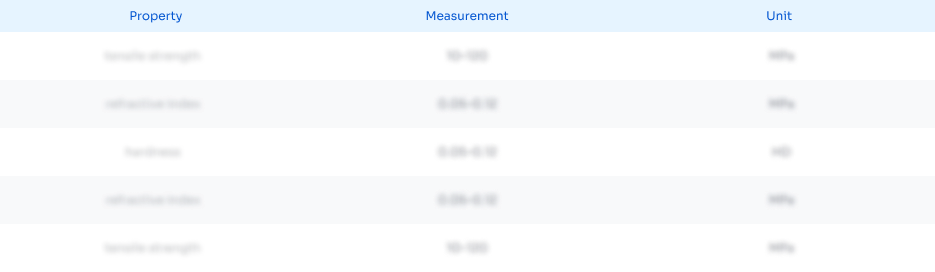
Abstract
Description
Claims
Application Information

- R&D Engineer
- R&D Manager
- IP Professional
- Industry Leading Data Capabilities
- Powerful AI technology
- Patent DNA Extraction
Browse by: Latest US Patents, China's latest patents, Technical Efficacy Thesaurus, Application Domain, Technology Topic, Popular Technical Reports.
© 2024 PatSnap. All rights reserved.Legal|Privacy policy|Modern Slavery Act Transparency Statement|Sitemap|About US| Contact US: help@patsnap.com