Quality improvement and control method for surface of copper alloy pipe
A surface quality and control method technology, which is applied in metal extrusion, manufacturing tools, metal processing equipment, etc., can solve the problems that the surface quality cannot be controlled, and the surface quality control of copper alloy tubes cannot be realized, so as to achieve less defects, long service life, The effect of improving quality
- Summary
- Abstract
- Description
- Claims
- Application Information
AI Technical Summary
Problems solved by technology
Method used
Examples
Embodiment 1
[0022] The copper alloy tube surface quality improvement and control method in this embodiment includes the following process steps in its manufacturing process:
[0023] (1) Soaking in degreasing aqueous solution: use an aqueous solution containing various components to soak the raw materials for the production of copper alloy tubes to achieve degreasing treatment and reduce the production bump of copper alloy tubes; the degreasing aqueous solution used is composed of the following components: Octadecyl dimethyl ammonium oxide, sodium lauryl polyoxyethylene ether sulfate, isopropanol, sodium alkylbenzene sulfonate, coconut oil alkyl glycol diamide and water, the above-mentioned components are calculated in parts by mass, They are: 10 parts of octadecyl dimethyl ammonium oxide, 12 parts of sodium lauryl polyoxyethylene ether sulfate, 8 parts of isopropanol, 20 parts of sodium alkylbenzene sulfonate, 10 parts of coconut oil alkyl glycol diamide 100 parts of water; the above com...
Embodiment 2
[0030] The copper alloy tube surface quality improvement and control method in this embodiment includes the following process steps in its manufacturing process:
[0031] (1) Soaking in degreasing aqueous solution: use an aqueous solution containing various components to soak the raw materials for the production of copper alloy tubes to achieve degreasing treatment and reduce the production bump of copper alloy tubes; the degreasing aqueous solution used is composed of the following components: Octadecyl dimethyl ammonium oxide, sodium lauryl polyoxyethylene ether sulfate, isopropanol, sodium alkylbenzene sulfonate, coconut oil alkyl glycol diamide and water, the above-mentioned components are calculated in parts by mass, They are: 15 parts of octadecyl dimethyl ammonium oxide, 18 parts of sodium lauryl polyoxyethylene ether sulfate, 14 parts of isopropanol, 30 parts of sodium alkylbenzene sulfonate, 14 parts of coconut oil alkyl glycol diamide 1. 170 parts of water; the above...
Embodiment 3
[0038] The copper alloy tube surface quality improvement and control method in this embodiment includes the following process steps in its manufacturing process:
[0039] (1) Soaking in degreasing aqueous solution: use an aqueous solution containing various components to soak the raw materials for the production of copper alloy tubes to achieve degreasing treatment and reduce the production bump of copper alloy tubes; the degreasing aqueous solution used is composed of the following components: Octadecyl dimethyl ammonium oxide, sodium lauryl polyoxyethylene ether sulfate, isopropanol, sodium alkylbenzene sulfonate, coconut oil alkyl glycol diamide and water, the above-mentioned components are calculated in parts by mass, They are: 25 parts of octadecyl dimethyl ammonium oxide, 24 parts of sodium lauryl polyoxyethylene ether sulfate, 20 parts of isopropanol, 40 parts of sodium alkylbenzene sulfonate, 18 parts of coconut oil alkyl glycol diamide , 240 parts of water; the above ...
PUM
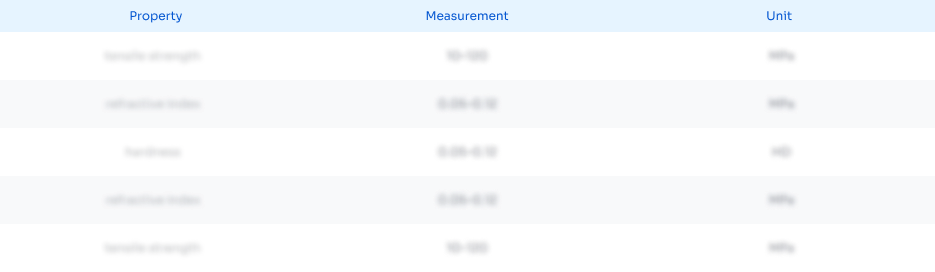
Abstract
Description
Claims
Application Information

- R&D
- Intellectual Property
- Life Sciences
- Materials
- Tech Scout
- Unparalleled Data Quality
- Higher Quality Content
- 60% Fewer Hallucinations
Browse by: Latest US Patents, China's latest patents, Technical Efficacy Thesaurus, Application Domain, Technology Topic, Popular Technical Reports.
© 2025 PatSnap. All rights reserved.Legal|Privacy policy|Modern Slavery Act Transparency Statement|Sitemap|About US| Contact US: help@patsnap.com