Vanadium extraction method for vanadium-bearing steel slag
A technology of steel slag and additives, applied in the field of vanadium extraction from vanadium-containing steel slag, and low-temperature sodium roasting-pressurized acid leaching technology to extract vanadium from vanadium-containing steel slag, can solve the problem that it is difficult to adapt to the resource characteristics of vanadium-containing steel slag and the limitation of popularization and application. , immature process and other problems, to achieve obvious effect of emission reduction, energy saving, energy saving effect.
- Summary
- Abstract
- Description
- Claims
- Application Information
AI Technical Summary
Problems solved by technology
Method used
Examples
Embodiment 1
[0020] Mix the vanadium-containing steel slag and sodium carbonate according to the mass ratio of 100:15, and divide the mixed material into two groups A and B (200g each). % ratio to add 4g additives, additives by 70wt% CaF 2 and 30wt% Na 3 AlF 6 composition. A and B groups of samples were respectively placed in a tubular electric furnace for roasting, and the roasting conditions were as follows: roasting temperature 650°C, roasting time 80min. The two groups of calcine were leached with hot water respectively, and the content of vanadium in the filtrate was determined. The leaching rate of vanadium in the samples of group A was 50%, and the leaching rate of vanadium in the samples of group B was 63%.
[0021] The calcined sand obtained after roasting the samples of Group B was placed in a reactor for pressure acid leaching, and compared with hot water leaching. The pressure acid leaching conditions are: pressure 0.8MPa, leaching temperature 90°C, mass concentration of su...
Embodiment 2
[0023] The experimental equipment is the same as in Example 1.
[0024] Mix the vanadium-containing steel slag and sodium carbonate according to the mass ratio of 100:10, and divide the mixed material into two groups A and B (each 200g). % ratio to add 5g additives, additives by 40wt% CaF 2 and 60wt% Na 3 AlF 6 composition. Then it is roasted, the roasting temperature is 700°C, and the roasting time is 70min. The two groups of calcined sand were leached by hot water respectively, the leaching rate of vanadium in group A samples was 58%, and the leaching rate of vanadium in group B samples was 68%.
[0025] The calcined sand obtained from group B samples was subjected to pressure acid leaching and hot water leaching tests. The pressure acid leaching conditions are: pressure 1.0MPa, leaching temperature 110°C, sulfuric acid mass concentration 22%, leaching time 80min, liquid-solid ratio 1.5mL / g; hot water leaching conditions are the same as in Example 1. During pressure ac...
Embodiment 3
[0027] The experimental equipment is the same as in Example 1.
[0028] Mix the vanadium-containing steel slag and sodium carbonate according to the mass ratio of 100:12, take the mixed material and divide it into two groups A and B (200g each). % ratio to add 6g additives, additives by 70wt% CaF 2 and 30wt% MnO 2 composition. Then it is roasted, the roasting temperature is 800°C, and the roasting time is 60min. The two groups of calcine were leached by hot water respectively, the leaching rate of vanadium in group A samples was 64%, and the leaching rate of vanadium in group B samples was 71%.
[0029] The calcined sand obtained from group B samples was subjected to pressure acid leaching and hot water leaching tests. The pressure acid leaching conditions are: pressure 1.2MPa, leaching temperature 130°C, sulfuric acid mass concentration 23%, leaching time 70min, liquid-solid ratio 1.4mL / g; hot water leaching conditions are the same as in Example 1. During pressure acid l...
PUM
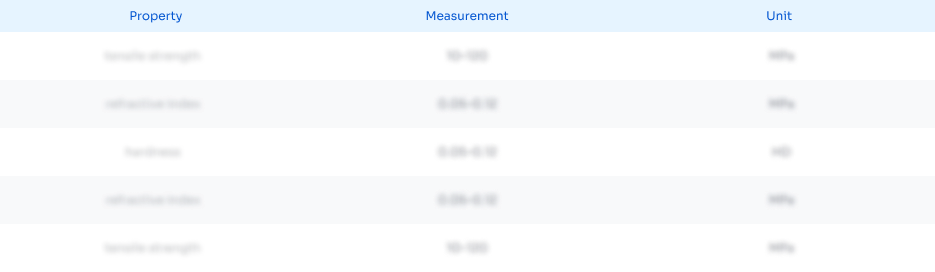
Abstract
Description
Claims
Application Information

- R&D Engineer
- R&D Manager
- IP Professional
- Industry Leading Data Capabilities
- Powerful AI technology
- Patent DNA Extraction
Browse by: Latest US Patents, China's latest patents, Technical Efficacy Thesaurus, Application Domain, Technology Topic, Popular Technical Reports.
© 2024 PatSnap. All rights reserved.Legal|Privacy policy|Modern Slavery Act Transparency Statement|Sitemap|About US| Contact US: help@patsnap.com