Vanadium-titanium iron ore utilization method
A vanadium ilmenite and pretreatment technology, applied in the field of metallurgy, can solve the problems of poor economy, difficulty in wide-scale promotion, waste of titanium resources, etc.
- Summary
- Abstract
- Description
- Claims
- Application Information
AI Technical Summary
Problems solved by technology
Method used
Image
Examples
Embodiment 1
[0035] Using vanadium-titanium iron concentrate as raw material, the main components and mass percentage of vanadium-titanium-iron concentrate are shown in Table 1, and the particle size distribution of the vanadium-titanium-iron concentrate is shown in Table 2, and Table 1 shows the The main components and content of the concentrate, Table 2 is the particle size distribution of a certain vanadium-titanium iron concentrate:
[0036] Table 1 The main components and content of a vanadium-titanium iron ore concentrate
[0037]
[0038]Note: TFe is the total mass percentage of iron elements in the sample.
[0039] Table 2 Particle size distribution of a vanadium-titanium iron ore concentrate
[0040]
[0041] The reducing agent is anthracite coal powder. The main chemical composition content and particle size distribution of anthracite coal powder are shown in Table 3 and Table 4 respectively. Table 3 shows the main components and content of anthracite coal powder, and Tabl...
Embodiment 2
[0054] Using vanadium-titanium iron concentrate as raw material, the main components and mass percentage of vanadium-titanium-iron concentrate are shown in Table 1, and the particle size distribution of the vanadium-titanium-iron concentrate is shown in Table 2.
[0055] Anthracite coal powder was used as the reducing agent, and the main chemical composition content and particle size distribution of the anthracite coal powder are shown in Table 3 and Table 4, respectively.
[0056] (1) Roasting pre-oxidation of vanadium-titanium iron concentrate
[0057] The above-mentioned vanadium-titanium iron concentrate was oxidized and roasted at 1000°C for 1.0 h to obtain a pretreated product. The content of FeO in the vanadium-titanium iron concentrate after oxidation and roasting was 1.04%, and the S content was 0.083%. The removal rate is 88.47%;
[0058] (2) Blocking of mixed materials
[0059] The pretreatment product is proportioned with anthracite coal powder and bentonite and ...
PUM
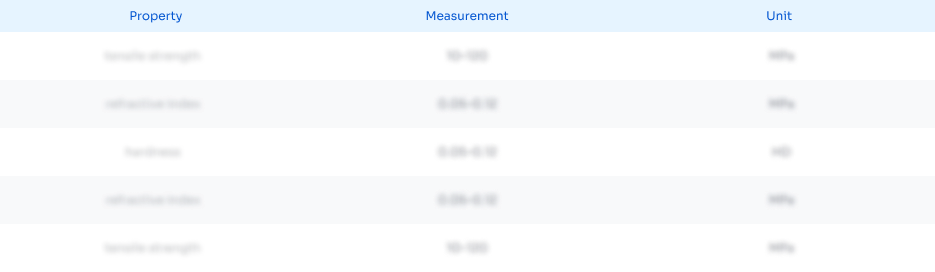
Abstract
Description
Claims
Application Information

- Generate Ideas
- Intellectual Property
- Life Sciences
- Materials
- Tech Scout
- Unparalleled Data Quality
- Higher Quality Content
- 60% Fewer Hallucinations
Browse by: Latest US Patents, China's latest patents, Technical Efficacy Thesaurus, Application Domain, Technology Topic, Popular Technical Reports.
© 2025 PatSnap. All rights reserved.Legal|Privacy policy|Modern Slavery Act Transparency Statement|Sitemap|About US| Contact US: help@patsnap.com