Spherical cage and spherical shell structure and technological processing method thereof
A technology of spherical shell structure and treatment method, applied in heat treatment furnaces, heat treatment equipment, metal material coating processes, etc., can solve the problems of inconsistent phase transition temperature, performance degradation of mechanical parts, automobile suffering, etc., to ensure ductility and hardness. requirements, high and low temperature impact toughness, and the effect of avoiding impact energy reduction
- Summary
- Abstract
- Description
- Claims
- Application Information
AI Technical Summary
Problems solved by technology
Method used
Image
Examples
Embodiment Construction
[0022] The following are specific embodiments of the present invention and in conjunction with the accompanying drawings, the technical solutions of the present invention are further described, but the present invention is not limited to these embodiments.
[0023] In the figure, the main shell 1; the outer frame body 2; the inner space body 3; the angled body 4; the outer rotation arc notch 5; Matching part 9; channel 10; channel chamfer 11; main body part 12; clamp first groove 13; clamp second groove 14;
[0024] Such as figure 1 and figure 2 As shown, the spherical shell structure of the ball cage includes a main housing 1, the main housing 1 is divided into an outer frame body 2 and an inner space body 3, steel balls are arranged in the inner space body 3, and on the surface of the outer frame body 2 There are six corners 4 along the circumference of the main housing 1, and there is an outwardly turning arc-shaped gap 5 between the two corners 4, and there is a buffer ...
PUM
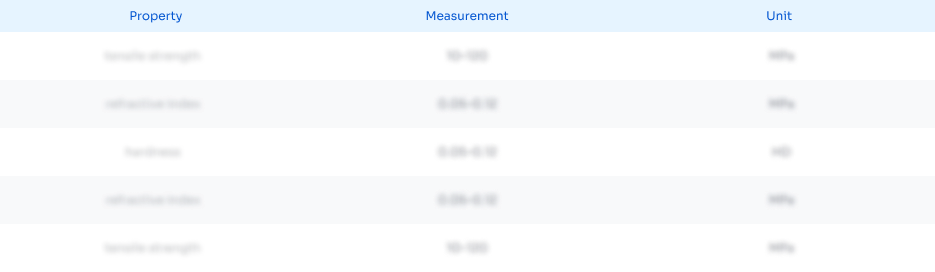
Abstract
Description
Claims
Application Information

- Generate Ideas
- Intellectual Property
- Life Sciences
- Materials
- Tech Scout
- Unparalleled Data Quality
- Higher Quality Content
- 60% Fewer Hallucinations
Browse by: Latest US Patents, China's latest patents, Technical Efficacy Thesaurus, Application Domain, Technology Topic, Popular Technical Reports.
© 2025 PatSnap. All rights reserved.Legal|Privacy policy|Modern Slavery Act Transparency Statement|Sitemap|About US| Contact US: help@patsnap.com