Omnipotent bed hydrogenation technology
A process, hydrogen technology, applied in the field of omnipotent bed processing) hydrogenation process, can solve the problems of increased device operation risk, complex mixing equipment, limited mixing uniformity, etc., achieve less air pollution and solid waste generation, and high resource utilization Efficiency, less air and less solid waste
- Summary
- Abstract
- Description
- Claims
- Application Information
AI Technical Summary
Problems solved by technology
Method used
Image
Examples
Embodiment 1
[0033] In this example, the omnipotent bed hydrogenation process using an empty cylinder structure reactor is used to process vacuum residue. For the process flow, see figure 1 , the processing raw material 2 is vacuum residue, and the properties of vacuum residue are shown in Table 1. Catalyst 3 is a Mo-Ni oil-soluble catalyst, and the addition amount accounts for 0.08wt% of the feed amount of residue. / Catalyst mixing equipment 1 performs mixing, the mixing temperature is 200° C., and the mixing time is 90 minutes, so that the concentration of the catalyst in the reaction material reaches a uniform state. The system also includes a raw material oil delivery pump 4, a circulating hydrogen compressor 5, a residual oil heating furnace 7, a hydrogen heating furnace 8, and transports mixed raw materials and fresh hydrogen 6 according to the connection shown in the figure, the primary reactor 11 and the secondary reactor 11. The catalyst concentration in the stage reactor 12 is 1...
Embodiment 2
[0040] In this embodiment, the omnipotent bed hydrogenation process of the internal circulation structure reactor is used to process the vacuum residue, and a reverse circulation pump 23 and a secondary reverse circulation pump 24 are added to the reactor. The process flow chart is shown in figure 2 , the processing raw material properties are the same as in Example 1. The catalyst is a Mo-Ni oil-soluble catalyst, the addition amount is 0.08wt%, the catalyst is mixed with the raw material oil, the mixing temperature is 200°C, and the mixing time is 90 minutes, so that the concentration of the catalyst in the reaction material reaches a uniform state and keeps the reaction The concentration of the catalyst in the vessel is 1000-1200ppm, the reaction temperature is 370°C, the reaction pressure is 16MPa, and the space velocity is 0.5h -1 , the hydrogen-to-oil ratio is 650, the vulcanizing agent is liquid sulfur, and the addition amount is 0.5%. The method of vulcanization while ...
Embodiment 3
[0043] Example 3: An example of residual oil fluidized bed hydrogenation process (comparative example).
[0044] Adopt ebullated bed hydrogenation process to process the raw material of embodiment 2, the operating temperature of ebullated bed, pressure, space velocity, reactor ten-ring ratio are the same as embodiment 2, the catalyst is a solid high-efficiency catalyst, and the catalyst volume in the reactor accounts for 50% of the reaction space %. The reaction products are dry gas, liquefied petroleum gas, naphtha, kerosene, diesel oil and wax oil fractions, wherein the yield of dry gas is 2.35%, and the yield of liquefied gas is 2.62%. The properties of oil phase products are summarized in Table 4.
[0045] Table 4 Summary of oil phase properties
[0046] project data C, wt% 92.91 H, wt% 5.71 S, wt% 0.42 N, wt% 0.86 Carbon residue, wt% 15.84 Asphaltenes, wt% 4.93 Toluene insoluble matter, wt% 1.79 Simulated distill...
PUM
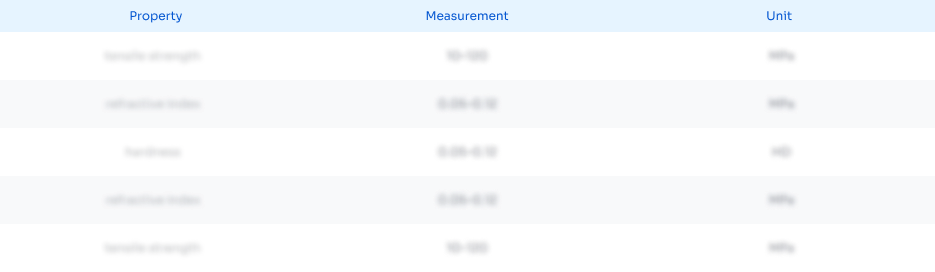
Abstract
Description
Claims
Application Information

- R&D
- Intellectual Property
- Life Sciences
- Materials
- Tech Scout
- Unparalleled Data Quality
- Higher Quality Content
- 60% Fewer Hallucinations
Browse by: Latest US Patents, China's latest patents, Technical Efficacy Thesaurus, Application Domain, Technology Topic, Popular Technical Reports.
© 2025 PatSnap. All rights reserved.Legal|Privacy policy|Modern Slavery Act Transparency Statement|Sitemap|About US| Contact US: help@patsnap.com