High-strength wear-resistant cable material and preparation method thereof
A cable material, high-strength technology, used in the field of wire and cable, can solve the problems of inability to meet market requirements, poor wear resistance, low strength, etc., and achieve the effect of easy popularization, long service life and high tensile strength.
- Summary
- Abstract
- Description
- Claims
- Application Information
AI Technical Summary
Problems solved by technology
Method used
Examples
Embodiment 1
[0021] A high-strength and wear-resistant cable material, which is made of the following raw materials in parts by weight: 85 parts of polyvinyl chloride, 24 parts of nitrile rubber, 18 parts of polyvinylidene fluoride, 10 parts of boronite, silicon carbide fiber 7 parts, 3 parts of polyhexamethylene adipate, 2 parts of triisononyl trimellitate, 4 parts of dimethyl methylphosphonate, 2 parts of carbon black, 1 part of polystyrene sulfonic acid, aluminum hydroxide 8 parts, 4 parts of magnesium stearate, 1 part of antioxidant, 1 part of anti-aging agent, 2 parts of polyethylene grafted maleic anhydride. Wherein, the anti-aging agent is anti-aging agent ODA; the antioxidant is antioxidant TPP.
[0022] In this embodiment, the preparation method of the high-strength wear-resistant cable material has the following steps:
[0023] 1) Weigh the solvatorite and silicon carbide fibers, put them into a ball mill, ball mill and mix for 2 hours, dry, and pass through a 100-mesh sieve to ...
Embodiment 2
[0029] A high-strength and wear-resistant cable material, which is made of the following raw materials in parts by weight: 86 parts of polyvinyl chloride, 25 parts of nitrile rubber, 19 parts of polyvinylidene fluoride, 11 parts of boronite, silicon carbide fiber 9 parts, 5 parts of polyhexamethylene adipate, 4 parts of triisononyl trimellitate, 7 parts of dimethyl methylphosphonate, 3 parts of carbon black, 1.2 parts of polystyrene sulfonic acid, aluminum hydroxide 9 parts, 6 parts of magnesium stearate, 2.8 parts of antioxidant, 1.7 parts of antioxidant, 3 parts of polyethylene grafted maleic anhydride. Wherein, the anti-aging agent is anti-aging agent ODA; the antioxidant is antioxidant TPP.
[0030] In this embodiment, the preparation method of the high-strength wear-resistant cable material has the following steps:
[0031] 1) Weigh the solvatorite and silicon carbide fibers, put them into a ball mill, ball mill and mix for 2 hours, dry, and pass through a 120-mesh sieve...
Embodiment 3
[0037] A high-strength and wear-resistant cable material, made of the following raw materials in parts by weight: 87 parts of polyvinyl chloride, 26 parts of nitrile rubber, 20 parts of polyvinylidene fluoride, 12 parts of boronite, silicon carbide fiber 9 parts, 4.5 parts of polyhexamethylene adipate, 3 parts of triisononyl trimellitate, 6 parts of dimethyl methylphosphonate, 4 parts of carbon black, 1.5 parts of polystyrene sulfonic acid, aluminum hydroxide 10 parts, 6 parts of magnesium stearate, 1.9 parts of antioxidant, 1.4 parts of antioxidant, 3.5 parts of polyethylene grafted maleic anhydride. Wherein, the anti-aging agent is anti-aging agent ODA; the antioxidant is antioxidant TPP.
[0038] In this embodiment, the preparation method of the high-strength wear-resistant cable material has the following steps:
[0039] 1) Weigh the solvatorite and silicon carbide fibers, put them into a ball mill, ball mill and mix for 2.5 hours, dry, and pass through a 120-mesh sieve t...
PUM
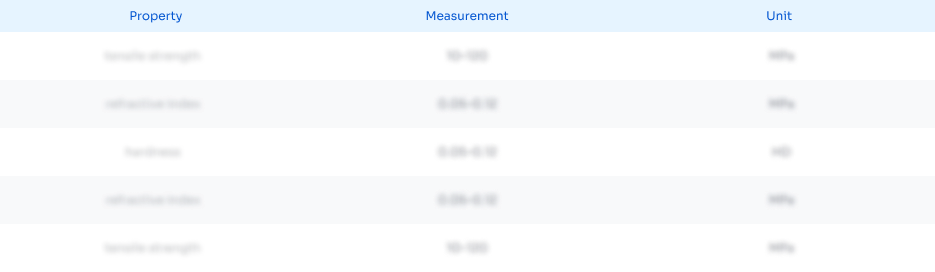
Abstract
Description
Claims
Application Information

- R&D
- Intellectual Property
- Life Sciences
- Materials
- Tech Scout
- Unparalleled Data Quality
- Higher Quality Content
- 60% Fewer Hallucinations
Browse by: Latest US Patents, China's latest patents, Technical Efficacy Thesaurus, Application Domain, Technology Topic, Popular Technical Reports.
© 2025 PatSnap. All rights reserved.Legal|Privacy policy|Modern Slavery Act Transparency Statement|Sitemap|About US| Contact US: help@patsnap.com