Methyl chloroacetate production method and device
A technology for the production of methyl chloroacetate, which is applied in the preparation of carboxylic acid esters, chemical instruments and methods, and the preparation of organic compounds, etc., can solve the problems of difficult post-processing rectification, serious discharge of three wastes, secondary pollution, etc., and achieve Avoid alkaline hydrolysis and hydrolysis consumption, protect the environment, reduce consumption and yield
- Summary
- Abstract
- Description
- Claims
- Application Information
AI Technical Summary
Problems solved by technology
Method used
Image
Examples
Embodiment 1
[0021] Embodiment 1 A kind of production method of methyl chloroacetate comprises the following steps,
[0022] a. Mix chloroacetic acid and methanol according to the molar ratio of 1:1.10-1:1.15 to form a mixed solution;
[0023] b. Evenly drop the mixed solution into the esterification reactor 2, and control the reaction temperature of the esterification reactor 2 to be 105-125°C;
[0024] c. A glass-lined packing tower 3 is arranged at the outlet of the esterification reactor 2, and after the esterification reactor 2 product is cooled, the water layer is separated through the water separation tank 5, and the separated methanol is recovered;
[0025] d. Drain the crude ester layer of the lower layer of the water separation tank 5 to the crude ester storage tank 7, and introduce the crude ester layer of the crude ester storage tank 7 into the rectification kettle 8 for rectification to obtain the finished product methyl chloroacetate.
[0026] In step d, the temperature is c...
Embodiment 2
[0035] Embodiment two A kind of production method of methyl chloroacetate, see figure 1 : including the following steps,
[0036] a. Mix chloroacetic acid and methanol according to the molar ratio of 1:1.10-1:1.15 to form a mixed solution;
[0037] b. Evenly drop the mixed solution into the esterification reactor 2, and control the reaction temperature of the esterification reactor 2 to be 105-125°C;
[0038] c. A glass-lined packing tower 3 is arranged at the outlet of the esterification reactor 2, and after the esterification reactor 2 product is cooled, the water layer is separated through the water separation tank 5, and the separated methanol is recovered;
[0039] d. Drain the crude ester layer of the lower layer of the water separation tank 5 to the crude ester storage tank 7, and introduce the crude ester layer of the crude ester storage tank 7 into the rectification kettle 8 for rectification to obtain the finished product methyl chloroacetate.
[0040] In step d, t...
PUM
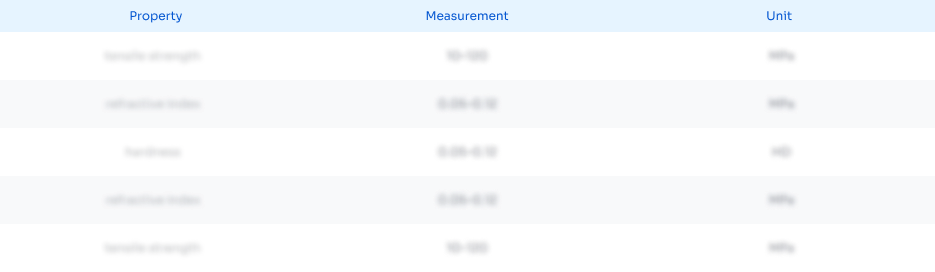
Abstract
Description
Claims
Application Information

- R&D
- Intellectual Property
- Life Sciences
- Materials
- Tech Scout
- Unparalleled Data Quality
- Higher Quality Content
- 60% Fewer Hallucinations
Browse by: Latest US Patents, China's latest patents, Technical Efficacy Thesaurus, Application Domain, Technology Topic, Popular Technical Reports.
© 2025 PatSnap. All rights reserved.Legal|Privacy policy|Modern Slavery Act Transparency Statement|Sitemap|About US| Contact US: help@patsnap.com