Cantilever crane beam installation process
An installation process and crane beam technology, which is applied in the field of installation and construction of steel structure workshops, can solve the problems of no uniform standard, random cutting, and legacy, and achieve the effect of avoiding economic losses and rapid installation and forming.
- Summary
- Abstract
- Description
- Claims
- Application Information
AI Technical Summary
Problems solved by technology
Method used
Examples
Embodiment Construction
[0015] As the best implementation mode of the present invention, aiming at the preliminary solution, combined with the experience of mechanical analysis and the operability of the construction method, a set of construction technology of "opening correction, post-adjustment and reinforcement" is proposed. The specific implementation plan is as follows:
[0016] The track length of the cantilever crane beam of this project is 162 meters, and there are 6 axes in total. First, one of the axes is selected for construction and installation correction test, and the selected part is 2 axes. During this test process, the crane girder components that have been installed must be disassembled, transported to the workshop for reprocessing, adjustment, and reinforcement, and then transported back to the factory building for re-hoisting.
[0017] Adjustment of the connection hole between the corbel column and the crane beam: Since there are two contact surfaces at both ends of the connection ...
PUM
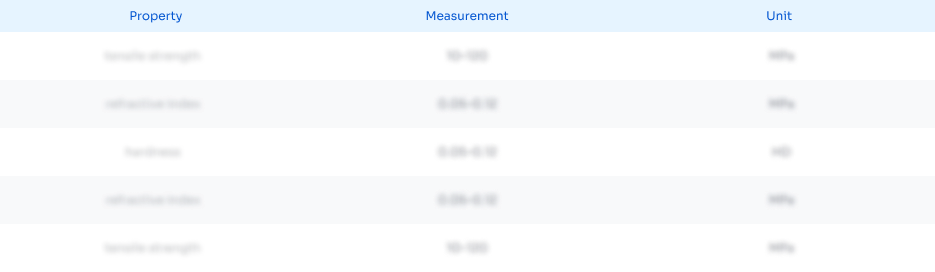
Abstract
Description
Claims
Application Information

- R&D
- Intellectual Property
- Life Sciences
- Materials
- Tech Scout
- Unparalleled Data Quality
- Higher Quality Content
- 60% Fewer Hallucinations
Browse by: Latest US Patents, China's latest patents, Technical Efficacy Thesaurus, Application Domain, Technology Topic, Popular Technical Reports.
© 2025 PatSnap. All rights reserved.Legal|Privacy policy|Modern Slavery Act Transparency Statement|Sitemap|About US| Contact US: help@patsnap.com