Organic waste gas recovery system
A technology of organic waste gas and recovery system, applied in the direction of gas treatment, steam condensation, membrane technology, etc., can solve problems such as easy fire, weld detachment, economic loss of users, etc.
- Summary
- Abstract
- Description
- Claims
- Application Information
AI Technical Summary
Problems solved by technology
Method used
Image
Examples
Embodiment Construction
[0014] The present invention will be further described in detail below in conjunction with the accompanying drawings and embodiments.
[0015] An organic waste gas recovery system, comprising a first adsorption bed 1, a second adsorption bed 2, a heating assembly, an adsorption assembly, a desorption assembly and a cooling assembly, the heating assembly includes a first steam coil arranged in the first adsorption bed 1 11 and the second steam coil 21 arranged in the second adsorption bed 2, the first steam coil 11 is provided with a first steam inlet 111 and a first steam outlet 112, and the second steam coil 21 is provided with a second steam inlet 211 and the second steam outlet 212, the first steam inlet 111 communicates with the output port of the external steam input device (not shown in the figure) through the first steam inlet pipe 12 provided with the first steam inlet control valve 121, the second steam inlet 211 The second steam inlet pipe 22 provided with the second...
PUM
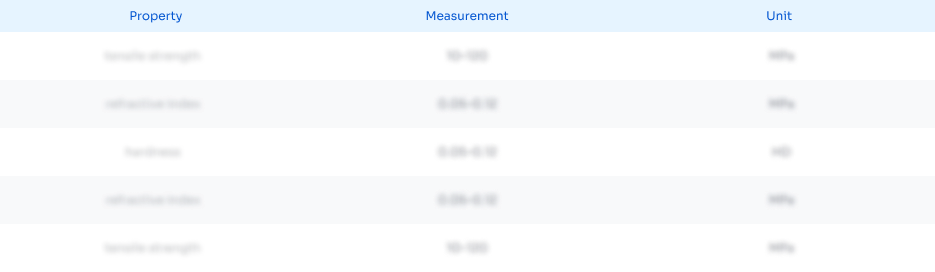
Abstract
Description
Claims
Application Information

- R&D
- Intellectual Property
- Life Sciences
- Materials
- Tech Scout
- Unparalleled Data Quality
- Higher Quality Content
- 60% Fewer Hallucinations
Browse by: Latest US Patents, China's latest patents, Technical Efficacy Thesaurus, Application Domain, Technology Topic, Popular Technical Reports.
© 2025 PatSnap. All rights reserved.Legal|Privacy policy|Modern Slavery Act Transparency Statement|Sitemap|About US| Contact US: help@patsnap.com