Car window lifting board forming process optimization method based on range analysis
A technology for raising and lowering windows and forming processes, applied in design optimization/simulation, special data processing applications, instruments, etc., can solve the problems of low assembly accuracy, high time and material cost, low efficiency, etc., and achieve time and material cost reduction. , the effect of shortening the development cycle and reducing the production cost
- Summary
- Abstract
- Description
- Claims
- Application Information
AI Technical Summary
Problems solved by technology
Method used
Image
Examples
Embodiment
[0020] Example: such as figure 1 As shown, a method for optimizing the forming process of the window lift plate based on the range analysis, the method includes the following steps:
[0021] (1) Determine the optimization target and optimization variables: Since the research object is a complex special-shaped bending stamping part, in order to ensure the overall assembly accuracy in the later stage, the maximum displacement of the part before and after forming is taken as the optimization target, and the maximum displacement is less than 0.7mm. Using conditions, the bending angle variation (△θ) of different sections of the part is not selected as the optimization target because the overall size of the part is mainly considered in the assembly process, and the detail size has little influence on the assembly accuracy; the optimization variables are sheet thickness A, Stamping speed B, friction factor C and die clearance D;
[0022] Table 1 Forming process parameter table
[0...
PUM
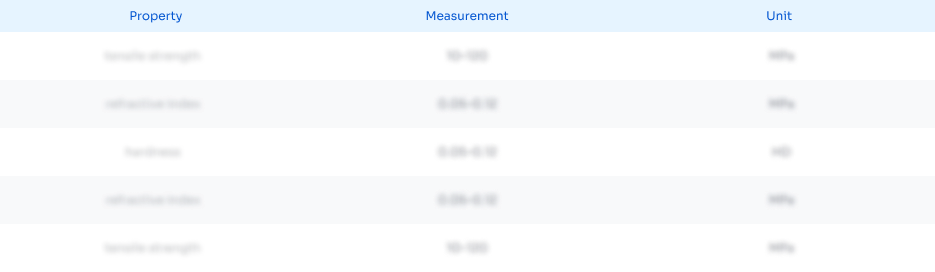
Abstract
Description
Claims
Application Information

- R&D
- Intellectual Property
- Life Sciences
- Materials
- Tech Scout
- Unparalleled Data Quality
- Higher Quality Content
- 60% Fewer Hallucinations
Browse by: Latest US Patents, China's latest patents, Technical Efficacy Thesaurus, Application Domain, Technology Topic, Popular Technical Reports.
© 2025 PatSnap. All rights reserved.Legal|Privacy policy|Modern Slavery Act Transparency Statement|Sitemap|About US| Contact US: help@patsnap.com