A green low-temperature rapid method for preparing phosphating film
A phosphating film and low temperature technology, which is applied in the field of material science and surface, can solve the problems of high energy consumption of phosphating treatment, increased phosphating cost, complicated phosphating process, etc., and achieves low cost, uniform and fine film layer, and phosphating formation high power effect
- Summary
- Abstract
- Description
- Claims
- Application Information
AI Technical Summary
Problems solved by technology
Method used
Examples
Embodiment 1
[0028] (1) In parts by weight, the following raw material components are weighed: 4 parts of zinc dihydrogen phosphate, 2 parts of manganese dihydrogen phosphate, 6 parts of zinc nitrate, 2 parts of phosphoric acid, 6 parts of 3.5wt% graphene oxide aqueous solution, 0.2 parts of PVP, 100 parts of water.
[0029] (2) Put the components of step (1) into the reaction kettle, use lye to adjust the pH to 2, then raise the temperature to 40°C, and stir evenly.
[0030] (3) Put the prepared phosphating treatment solution into the phosphating tank, raise the temperature of phosphating treatment to 28°C, then immerse the steel test piece in it, process for 5 minutes, rinse with water and dry to obtain phosphating processed specimens.
[0031] There is basically no phosphating residue in the phosphating pool after phosphating, which shows that the success rate of phosphating of the test piece is high.
[0032] The present invention uses the GB6458-86 neutral salt spray test to test th...
Embodiment 2
[0039] (1) Take the following raw material components according to the weight ratio: 8 parts of zinc dihydrogen phosphate, 4 parts of zinc nitrate, 3 parts of calcium phosphate, 2.5 parts of phosphoric acid, 0.05 parts of graphene oxide powder, 0.2 parts of APEO, and 100 parts of water.
[0040] (2) Put each component into the reaction kettle, use lye to adjust the pH to 3, then raise the temperature to 30°C, and stir evenly.
[0041] (3) Put the prepared phosphating treatment liquid into the phosphating tank, raise the temperature of phosphating treatment to 30°C, then immerse the steel test piece in it, process for 4 minutes, rinse with water and dry to obtain phosphating processed specimens.
[0042]The present invention uses the GB6458-86 neutral salt spray test to test the anti-corrosion performance of the phosphating film.
[0043] The appearance of the phosphating film obtained in Example 2 is gray and bright, the film layer is fine and smooth, and the film thickness i...
Embodiment 3
[0046] (1) Take the following raw material components by weight ratio: 7 parts of zinc dihydrogen phosphate, 6 parts of zinc nitrate, 1 part of phosphoric acid, 0.2 parts of 2.2wt% graphene oxide aqueous solution, 0.2 parts of OP-10 emulsifier, TX- 10 0.3 parts, 120 parts of water
[0047] (2) Put each component into the reaction kettle, use lye to adjust the pH to 3, then raise the temperature to 25°C, and stir evenly.
[0048] (3) Put the prepared phosphating treatment liquid into the phosphating tank, raise the temperature of phosphating treatment to 20°C, then immerse the steel test piece in it, process for 10 minutes, rinse with water and dry to obtain phosphating processed specimens.
[0049] The present invention uses the GB6458-86 neutral salt spray test to test the anti-corrosion performance of the phosphating film.
[0050] The appearance of the phosphating film obtained in Example 3 is gray and bright, the film layer is fine and smooth, and the film thickness is 3...
PUM
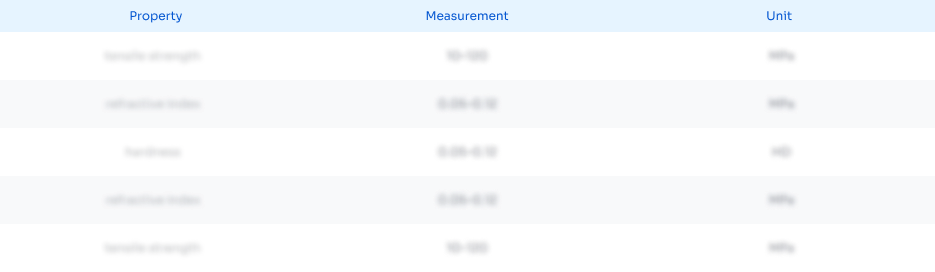
Abstract
Description
Claims
Application Information

- R&D Engineer
- R&D Manager
- IP Professional
- Industry Leading Data Capabilities
- Powerful AI technology
- Patent DNA Extraction
Browse by: Latest US Patents, China's latest patents, Technical Efficacy Thesaurus, Application Domain, Technology Topic, Popular Technical Reports.
© 2024 PatSnap. All rights reserved.Legal|Privacy policy|Modern Slavery Act Transparency Statement|Sitemap|About US| Contact US: help@patsnap.com