Graphene wear-resistant coating
A wear-resistant coating, graphene technology, applied in polyamide coatings, epoxy resin coatings, coatings, etc., to achieve good heat resistance and thermal conductivity, prevent chemical degradation, reduce friction coefficient and wear rate.
- Summary
- Abstract
- Description
- Claims
- Application Information
AI Technical Summary
Problems solved by technology
Method used
Image
Examples
Embodiment 1
[0016] After weighing each raw material according to the proportioning ratio in Table 1, stir and mix at 1600-2000 rpm. The graphene wear-resistant coating can be obtained;
[0017] The raw material formula of table 1 graphene wear-resistant coating
[0018]
[0019]
Embodiment 2
[0021] Stir and mix after weighing each raw material by the proportioning of Table 2 to obtain the graphene wear-resistant coating;
[0022] The raw material formula of table 2 graphene wear-resistant coating
[0023]
[0024]
Embodiment 3
[0026] Stir and mix after weighing each raw material by the proportioning of Table 3 to obtain the graphene wear-resistant coating;
[0027] The raw material formula of table 3 graphene wear-resistant coating
[0028]
[0029]
PUM
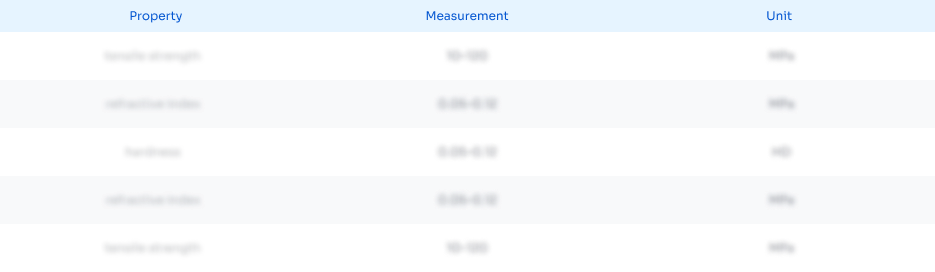
Abstract
Description
Claims
Application Information

- R&D Engineer
- R&D Manager
- IP Professional
- Industry Leading Data Capabilities
- Powerful AI technology
- Patent DNA Extraction
Browse by: Latest US Patents, China's latest patents, Technical Efficacy Thesaurus, Application Domain, Technology Topic, Popular Technical Reports.
© 2024 PatSnap. All rights reserved.Legal|Privacy policy|Modern Slavery Act Transparency Statement|Sitemap|About US| Contact US: help@patsnap.com