Well cementing slurry capable of preventing CO2 and H2S corrosion
A technology for cementing cement slurry and cement slurry, which can be used in wellbore/well components, drilling composition, earth-moving drilling, etc., and can solve the problems of increased permeability, decreased compressive strength, and shortened life of oil and gas wells. , to achieve the effect of improving compressive strength, eliminating tiny bubbles and prolonging setting time
- Summary
- Abstract
- Description
- Claims
- Application Information
AI Technical Summary
Problems solved by technology
Method used
Image
Examples
Embodiment 1
[0015] An anti-CO 2 、H 2 S corrosion cementing cement slurry, which is composed of water and cement with a mass ratio (water-cement ratio) of 0.45:1, wherein the cement comes from the following raw materials: 100 mass units of G-grade high sulfate-resistant oil well cement , 12 mass units of fine cement, 1 mass unit of dispersant SXY, 1.2 mass units of fluid loss reducer BXF-200L, 6 mass units of micro-silicon JM-1, 8 mass units of fly ash , 1.2 mass units of expansion agent M53S, 9 mass units of latex BCT-800L, 1 mass unit of water-soluble methylated urea-formaldehyde resin, 1.5 mass units of early strength agent CK21, 0.1 mass unit of retarder Agent SN-2, 0.6 mass units of defoamer D50.
[0016] The anti-CO 2 、H 2 The preparation method of S corrosion cementing cement slurry is: first mix the water-soluble methyl etherified urea-formaldehyde resin and water evenly, and then make the mixed solution with fluid loss reducer BXF-200L, latex BCT-800L, retarder SN-2 and defoa...
Embodiment 2
[0018] An anti-CO 2 、H 2 S corrosion cementing cement slurry, which is composed of water and cement with a mass ratio (water-cement ratio) of 0.45:1, wherein the cement comes from the following raw materials: 100 mass units of G-grade high sulfate-resistant oil well cement , 15 mass units of fine cement, 1.5 mass units of dispersant SXY, 1.3 mass units of fluid loss reducer BXF-200L, 5 mass units of micro-silicon JM-1, 8 mass units of fly ash , 1.3 mass units of expansion agent M53S, 6 mass units of latex BCT-800L, 1.4 mass units of water-soluble maleic anhydride modified epoxy resin, 2.5 mass units of early strength agent CK21, 0.2 mass units retarder SN-2, 0.7 mass units of defoamer D50.
[0019] The anti-CO 2 、H 2 The preparation method of S corrosion cementing cement slurry is the same as that in Example 1. Code name recipe 2.
Embodiment 3
[0021] An anti-CO 2 、H 2 S corrosion cementing cement slurry, which is composed of water and cement with a mass ratio (water-cement ratio) of 0.45:1, wherein the cement comes from the following raw materials: 100 mass units of G-grade high sulfate-resistant oil well cement , 17 mass units of fine cement, 1.8 mass units of dispersant SXY, 1.2 mass units of fluid loss reducer BXF-200L, 7 mass units of micro-silicon JM-1, 6 mass units of fly ash , 1.7 mass units of expansion agent M53S, 7 mass units of latex BCT-800L, 1.3 mass units of water-soluble acrylic modified alkyd resin, 2 mass units of early strength agent CK21, 0.2 mass units of retarder Coagulant SN-2, 0.7 mass units of defoamer D50.
[0022] The anti-CO 2 、H 2 The preparation method of S corrosion cementing cement slurry is the same as that in Example 1. Code name recipe 3.
[0023] In order to study the performance of the present invention, the designer did a comparative experiment with formula 1, formula 2, fo...
PUM
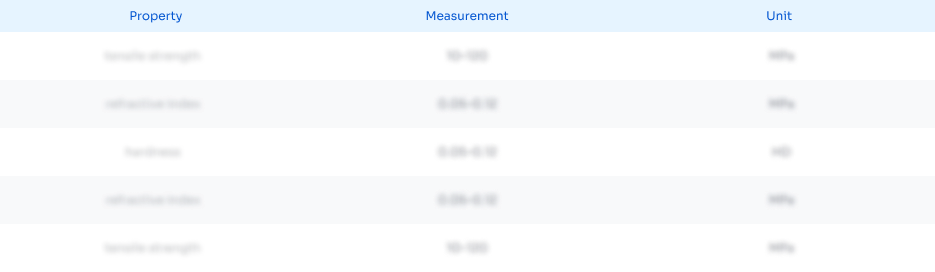
Abstract
Description
Claims
Application Information

- R&D
- Intellectual Property
- Life Sciences
- Materials
- Tech Scout
- Unparalleled Data Quality
- Higher Quality Content
- 60% Fewer Hallucinations
Browse by: Latest US Patents, China's latest patents, Technical Efficacy Thesaurus, Application Domain, Technology Topic, Popular Technical Reports.
© 2025 PatSnap. All rights reserved.Legal|Privacy policy|Modern Slavery Act Transparency Statement|Sitemap|About US| Contact US: help@patsnap.com