Production method of antibacterial and flame-retarding Dacron fabric for suitcases and bags
A technology for luggage fabrics and flame-retardant polyester, applied in the field of preparation of functional luggage materials, can solve the problems of large smoke generation, molten droplets, corrosion, etc., achieve good flame-retardant effect, improve washing resistance, and flame-retardant good effect
- Summary
- Abstract
- Description
- Claims
- Application Information
AI Technical Summary
Problems solved by technology
Method used
Image
Examples
Embodiment 1
[0034] Prepare antibacterial and flame retardant working solution. Add flame retardant (composed of aluminum dihydrogen tripolyphosphate: antimony trioxide molar ratio 3:1) into the water and disperse fully. Use HAc to adjust the pH value to 6.5, add 80% of the total water; then add antibacterial finishing agent (dichlorophen), stir, and dilute with the remaining amount of water to prepare a flame retardant concentration of 160g / L and an antibacterial agent concentration It is a 30g / L antibacterial and flame retardant finishing solution.
[0035] (2) Process flow
[0036] Two dipping and two padding (residual rate of 70%), drying (100°C, 2min), curing (180°C, 120s) and then washing with water, drying (100°C, 3min).
[0037] (3) Test the antibacterial, flame retardant and tear strength of the luggage fabric, the results are shown in Table 1.
[0038] Table 1 Antibacterial, flame retardant and strength loss of luggage fabrics
[0039]
Embodiment 2
[0041] (1) Prepare antibacterial and flame retardant working solution. Add water to flame retardant (composed of triphosphate (2,3-dibromopropyl): antimony pentoxide 2:1), and fully disperse. Use HAc to adjust the pH value to 6.5, add 60% water of the total water, then add antibacterial finishing agent (1-hydroxy-3 methyl-4 cumene), stir, add the remaining water to dilute, and prepare the antibacterial Combustion agent concentration is 175g / L and antibacterial agent concentration is the antibacterial flame retardant finishing liquid of 35g / L.
[0042] (2) Process flow
[0043] Two dipping and two padding (residual rate of 70%), drying (100°C, 2min), curing (175°C, 120s), then washing with water, drying (120°C, 2min).
[0044](3) Test the antibacterial, flame retardant and tear strength of the luggage fabric, the results are shown in Table 2.
[0045] Table 2 Antibacterial, flame retardant and strength loss of luggage fabrics
[0046]
Embodiment 3
[0048] (1) Prepare antibacterial and flame retardant working solution. Add a flame retardant (composed of polyphosphate amine: antimony trioxide molar ratio 4:1) to the water and fully disperse it. use Na 2 CO 3 Adjust the pH value to 7.5, add 50% water of the total water, then add antibacterial finishing agent (p-chloro-m-xylenol), stir, add the remaining water to dilute, and prepare the flame retardant with a concentration of 170g / L and antibacterial An antibacterial and flame retardant finishing solution with an agent concentration of 30g / L.
[0049] (2) Process flow
[0050] Two dipping and two padding (the excess rate is 70%), drying (100°C, 2min), baking (180°C, 120s), then washing with water, and drying (150°C, 1min).
[0051] (3) Test the antibacterial, flame retardant and tear strength of the luggage fabric, the results are shown in Table 3.
[0052] Table 3 Antibacterial, flame retardant and strength loss of luggage fabrics
[0053]
PUM
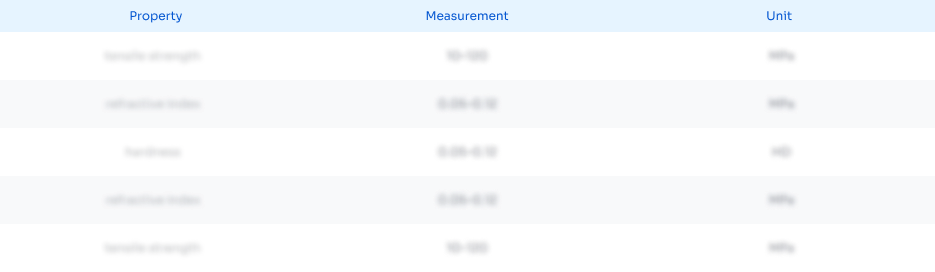
Abstract
Description
Claims
Application Information

- R&D
- Intellectual Property
- Life Sciences
- Materials
- Tech Scout
- Unparalleled Data Quality
- Higher Quality Content
- 60% Fewer Hallucinations
Browse by: Latest US Patents, China's latest patents, Technical Efficacy Thesaurus, Application Domain, Technology Topic, Popular Technical Reports.
© 2025 PatSnap. All rights reserved.Legal|Privacy policy|Modern Slavery Act Transparency Statement|Sitemap|About US| Contact US: help@patsnap.com