Powdered ink for electronic photographic development and preparation method thereof
A technology of electrophotography and toner, applied in the directions of developer, electrography, optics, etc., can solve the problems of high equipment requirements and complicated mixing methods, and achieve low equipment requirements, small residue, simple process and operation Effect
- Summary
- Abstract
- Description
- Claims
- Application Information
AI Technical Summary
Problems solved by technology
Method used
Image
Examples
preparation example Construction
[0051] Preparation of linear polyester resin:
[0052] Method 1: The following parts by weight are 160 parts of terephthalic acid; 100 parts of isophthalic acid; 200 parts of ethylene glycol; React for 3 hours and remove the water generated by the reaction, then carry out vacuum distillation on the system for 1 hour, keep the vacuum at 150 Pa, stop the reaction, cool down and discharge to obtain linear polyester resin E1. Tg (glass transition temperature of resin) = 54°C, Mn (number average molecular weight) = 3500, Mw (weight average molecular weight) = 28000.
[0053] Method 2: The following parts by weight, 130 parts of terephthalic acid; 130 parts of isophthalic acid; 200 parts of ethylene glycol; React for 3 hours and remove the water generated by the reaction, then carry out vacuum distillation on the system for 1.5 hours, keep the vacuum at 130Pa, stop the reaction, cool down and discharge to obtain linear polyester resin E2. Tg (glass transition temperature of resin)...
Embodiment 1
[0057] Mix the following vinyl monomers and linear polyesters, pigments, waxes and charge control agents in the following parts by weight
[0058]
[0059]
[0060] Disperse the above components into an oil phase with a bead mill at room temperature, add 4 parts of benzoyl peroxide as an oil-soluble initiator, and fully disperse for 30 minutes to obtain a monomer oil phase dispersion;
[0061] Dissolve 13 parts by mass of magnesium chloride in 100 parts by mass of deionized water, then slowly add 200 parts by mass to an aqueous solution in which 8 parts by mass of sodium hydroxide has been dissolved, disperse at high speed for 1 hour, and age ultrasonically at room temperature for 4 hours to obtain hydrogen Magnesium Oxide Suspending and Dispersing Agent.
[0062] Add the prepared monomer oil phase to the above-mentioned magnesium hydroxide suspension dispersant containing magnesium chloride electrolyte, and use a high-speed disperser to shear at 4000 rpm for 5 minutes t...
Embodiment 2
[0065] Mix the following vinyl monomers and linear polyesters, pigments, waxes and charge control agents in the following parts by weight
[0066]
[0067]
[0068] Disperse the above components into an oil phase with a bead mill at room temperature, add 4 parts of benzoyl peroxide as an oil-soluble initiator, and fully disperse for 30 minutes to obtain a monomer oil phase dispersion;
[0069] Dissolve 11 parts by mass of magnesium chloride in 100 parts by mass of deionized water, then slowly add 200 parts by mass into an aqueous solution in which 8 parts by mass of sodium hydroxide has been dissolved, disperse at high speed for 1.5 hours, and age ultrasonically at room temperature for 3 hours to obtain Magnesium Hydroxide Suspending and Dispersing Agent.
[0070] Add the prepared monomer oil phase to the above-mentioned magnesium hydroxide suspension dispersant containing magnesium chloride electrolyte, and use a high-speed disperser to shear at 4000 rpm for 5 minutes t...
PUM
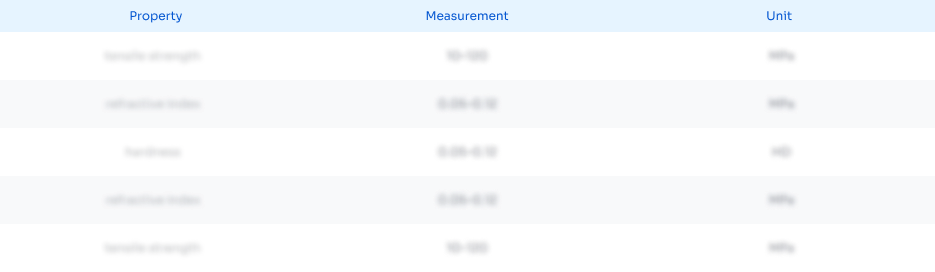
Abstract
Description
Claims
Application Information

- R&D
- Intellectual Property
- Life Sciences
- Materials
- Tech Scout
- Unparalleled Data Quality
- Higher Quality Content
- 60% Fewer Hallucinations
Browse by: Latest US Patents, China's latest patents, Technical Efficacy Thesaurus, Application Domain, Technology Topic, Popular Technical Reports.
© 2025 PatSnap. All rights reserved.Legal|Privacy policy|Modern Slavery Act Transparency Statement|Sitemap|About US| Contact US: help@patsnap.com