Two-dimension ultra-precision positioning platform driven by voice coil motor
A technology of voice coil motor and positioning platform, which is applied in the direction of machines/supports, supporting machines, mechanical equipment, etc., can solve the problems of slow speed response, complex control system, and low bearing capacity, so as to reduce transmission errors and The effect of platform volume and strong carrying capacity
- Summary
- Abstract
- Description
- Claims
- Application Information
AI Technical Summary
Problems solved by technology
Method used
Image
Examples
Embodiment Construction
[0027] The present invention will be further described below in conjunction with specific embodiment:
[0028] See attached Figure 1-2 As shown, a voice coil motor-driven two-dimensional ultra-precision positioning platform described in this embodiment includes a platform base 1, a mobile platform 2, first and second guide rails 3, 4, first and second voice coil motors 5, 6 , the first and second incremental grating rulers 9, 10, DC driver 11 and controller 12.
[0029] Wherein, the platform base 1 is composed of a horizontal base 101 and a vertical base 102 , and the first voice coil motor 5 is installed on the horizontal base 101 .
[0030] The mobile platform 2 includes a vertical mobile platform 7 and a forward and backward mobile platform 8 .
[0031] The up and down moving platform 7 is fixedly connected above the first voice coil motor 5 and is driven by the first voice coil motor 5 to move up and down along the first guide rail 3 laid on the vertical base 102, and i...
PUM
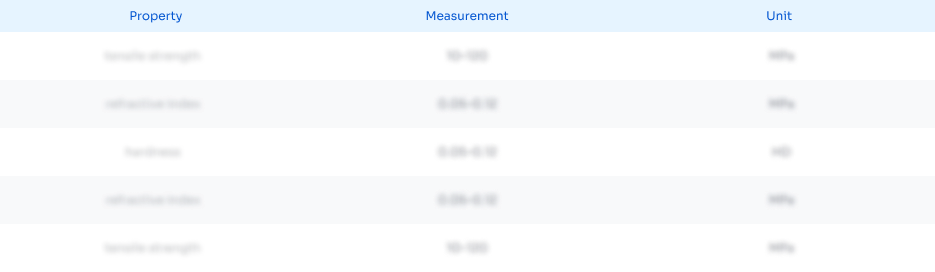
Abstract
Description
Claims
Application Information

- R&D
- Intellectual Property
- Life Sciences
- Materials
- Tech Scout
- Unparalleled Data Quality
- Higher Quality Content
- 60% Fewer Hallucinations
Browse by: Latest US Patents, China's latest patents, Technical Efficacy Thesaurus, Application Domain, Technology Topic, Popular Technical Reports.
© 2025 PatSnap. All rights reserved.Legal|Privacy policy|Modern Slavery Act Transparency Statement|Sitemap|About US| Contact US: help@patsnap.com