EMC-demand-requiring permanent magnet direct current motor of capacitor triangle-type connection structure
A technology of permanent magnet DC connection method, which is applied in the manufacture of motor generators, structural connections, electrical components, etc., can solve the problems of motor processing, high manufacturing cost, complicated processing technology, time-consuming and labor-intensive, etc., and achieve high electromagnetic compatibility Requirements, saving personnel, simple structure effect
- Summary
- Abstract
- Description
- Claims
- Application Information
AI Technical Summary
Problems solved by technology
Method used
Image
Examples
Embodiment 1
[0019] like figure 1 and image 3 As shown, the present invention provides a permanent magnet DC motor with a capacitor delta connection structure that meets EMC requirements, including a stator assembly 1, a rotor assembly 2 and a rear cover assembly 3, and the rotor assembly 2 is arranged in the stator assembly 1 , the end cover assembly 3 is arranged at one end of the stator assembly 1; the rotor assembly 2 includes a motor shaft 4, an oil baffle plate 5, a commutator 6, a piezoresistor 7, a PCB board 14, a rotor coil 10, an iron Core 11, copper sleeve 12 and gasket 13; the oil baffle plate 5, commutator 6, varistor 7, PCB board 14, iron core 11, copper sleeve 12 and gasket 13 are arranged on the motor shaft 4 in sequence , the rotor coil 10 is wound between the slots of the rotor core 11; the PCB board 14 is provided with three chip capacitors 15, and the chip capacitors 15 are connected to the commutator 6 through the PCB board 14; The two patch capacitors are connected...
PUM
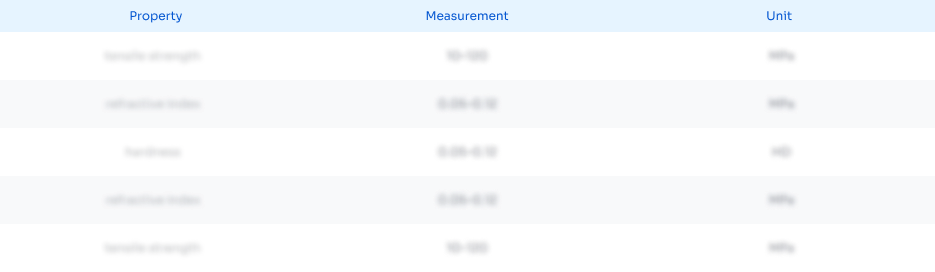
Abstract
Description
Claims
Application Information

- R&D
- Intellectual Property
- Life Sciences
- Materials
- Tech Scout
- Unparalleled Data Quality
- Higher Quality Content
- 60% Fewer Hallucinations
Browse by: Latest US Patents, China's latest patents, Technical Efficacy Thesaurus, Application Domain, Technology Topic, Popular Technical Reports.
© 2025 PatSnap. All rights reserved.Legal|Privacy policy|Modern Slavery Act Transparency Statement|Sitemap|About US| Contact US: help@patsnap.com