Method for refining isophthalonitrile
A technology of isophthalonitrile and distillation kettle, which is applied in the purification/separation of carboxylic acid nitrile, organic chemistry, etc., can solve the problems of high energy consumption, difficulty in obtaining, high price, etc., and achieve increased yield, reduced content, and improved product quality. quality effect
- Summary
- Abstract
- Description
- Claims
- Application Information
AI Technical Summary
Problems solved by technology
Method used
Image
Examples
Embodiment 1
[0024] A kind of method that is used for isophthalonitrile refining, its technological process is as figure 1 As shown, the isophthalonitrile crude product obtained by thin-wall trapping or water spray trapping is used as raw material, and the solid powdery raw material is added in still 1, and the heating of the still adopts heat transfer oil. The crude phthalonitrile is slowly melted from solid to liquid. After the temperature of the kettle is raised to 180°C, the vacuum is turned on, and the vacuum degree is raised to above 0.08MPa, and stirring is started. Continue heating until the temperature of the kettle reaches 210°C, and the product begins to evaporate, and the vacuum degree is increased to above 0.095MPa. When the temperature of the top of the kettle is raised to 250°C, turn off the vacuum, stop feeding the heat transfer oil, and cool down the distillation kettle. Regularly open the valve at the bottom of the still to discharge the distillation residue in the still....
Embodiment 2
[0028] A method for refining isophthalonitrile, using the crude isophthalonitrile obtained by thin-wall capture as a raw material, and introducing the solid powdery raw material into a still. In this embodiment, the still adopts a still-type The reactor is heated by heat conduction oil, and the temperature in the kettle is controlled at 170°C. The crude product is slowly melted from solid to liquid. After it is completely melted, the vacuum is turned on and the stirring is turned on, and the vacuum degree is increased to above 0.085MPa. Continue to heat until the temperature of the still reaches 206°C, and the product begins to evaporate, and the vacuum degree is increased to above 0.095MPa, continue to heat up, and stop when the temperature of the top of the still is 250°C, the raw materials are stirred in the still by propulsion, and the liquid in the still boils After that, isophthalonitrile turns into gas and is steamed out from the distillation tank. The distilled isophtha...
Embodiment 3
[0032] A method for refining isophthalonitrile, using the crude isophthalonitrile obtained by thin-wall capture as a raw material, and introducing the solid powdery raw material into a still. In this embodiment, the still adopts a still-type The reactor is heated by heat conduction oil, and the temperature in the kettle is controlled at 240°C. The crude product is slowly melted from solid to liquid. After it is completely melted, turn on the water flushing vacuum pump, control the vacuum degree of the reaction system to 0.08MPa, turn on stirring and continue to heat up, and distill Stop when the temperature at the top of the still is 260°C, the raw materials are stirred by anchor in the distillation kettle, after the liquid in the kettle boils, isophthalonitrile turns into gas and evaporates from the distillation kettle, and the distilled isophthalonitrile steam passes through the column The tubular heat exchanger is cooled to 180°C, and then introduced into the receiving kettl...
PUM
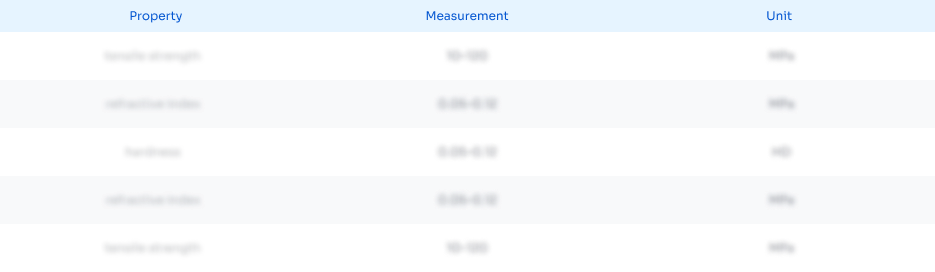
Abstract
Description
Claims
Application Information

- Generate Ideas
- Intellectual Property
- Life Sciences
- Materials
- Tech Scout
- Unparalleled Data Quality
- Higher Quality Content
- 60% Fewer Hallucinations
Browse by: Latest US Patents, China's latest patents, Technical Efficacy Thesaurus, Application Domain, Technology Topic, Popular Technical Reports.
© 2025 PatSnap. All rights reserved.Legal|Privacy policy|Modern Slavery Act Transparency Statement|Sitemap|About US| Contact US: help@patsnap.com