Processing method of cotton and copper alginate blended yarn
A processing method and technology of copper alginate, which are applied in the directions of yarn, textile and paper making, can solve the problems of low spinnable yarn count, low design content and poor spinnability of the yarn, and achieve high production efficiency, less neps, good dry effect
- Summary
- Abstract
- Description
- Claims
- Application Information
AI Technical Summary
Problems solved by technology
Method used
Image
Examples
Embodiment 1
[0021] Embodiment 1: the pretreatment process of alginate copper fiber
[0022] Copper alginate fibers are brittle and broken, and there are problems such as fiber cohesion, low strength, high brittleness, and poor spinnability.
[0023] Conventional practice (such as CN 105012999A) adopts direct blending of copper alginate fiber and absorbent cotton. Although the blended yarn can be endowed with good antibacterial properties, the strength and spinning conditions of the yarn have not been improved. The blended yarn has the antibacterial property of copper alginate fiber, but it does not endow the blended yarn with processability.
[0024] In this example, the copper alginate fiber is pretreated to improve its yarn-forming performance. The main parameters of the copper alginate fiber pretreatment, that is, the health care treatment include additives, water temperature, the ratio of additives to water, the ratio of health care solution to fiber, There are five factors of health...
Embodiment 2
[0047] Embodiment 2: the setting of opening and cleaning, carding process
[0048] Based on the fact that the alginate copper fiber is brittle and broken, there are problems such as fiber cohesion, low strength, high brittleness, and poor spinnability. Conduct experiments to reduce the impact strength of alginate copper fiber and maximize the loss of alginate copper fiber to increase the production rate of alginate copper fiber. The main parameter of the opening and cleaning process is the distance between the impact point and the holding point The main parameters of carding are the height of the cotton feeding board, the speed of the carding part and the speed of the flat board.
[0049] (1) The opening and cleaning process includes: processing the mixed fibers through the plucking machine, the mixing opener, the roller card opening machine, the vibrating cotton feeding box and the single hand lapping machine in sequence. All beaters of roller card opener and single beater l...
Embodiment 3
[0052] Example 3: Processing of 7.29tex cotton / copper alginate fiber 97 / 3 blended yarn for high-grade underwear
[0053] The 7.29tex cotton / copper alginate fiber 97 / 3 blended yarn for high-grade underwear produced in this embodiment uses 6800-7200Nm of raw cotton. The specific implementation process is as follows: the health liquid: alginate copper fiber is treated for 24 hours at a ratio of 1:10, and then mixed with the slivers that have been opened and removed and broken into bales on the bale grabbing machine; The cotton cleaning process adopts a half-grip striking distance, the distance between the striking point and the holding point is 35mm, and the striking speed of the beater of the single beater lapping machine is 720r / min; the carding process raises the cotton board by 12mm; The piece speed is 730rpm for the licker-in roller, 270rpm for the cylinder, and 22rpm for the doffer; the flat plate speed is 70mmpm; the twist coefficient of the roving in the roving process is...
PUM
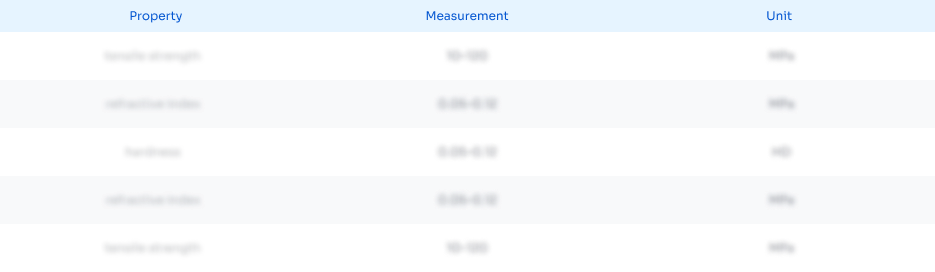
Abstract
Description
Claims
Application Information

- R&D
- Intellectual Property
- Life Sciences
- Materials
- Tech Scout
- Unparalleled Data Quality
- Higher Quality Content
- 60% Fewer Hallucinations
Browse by: Latest US Patents, China's latest patents, Technical Efficacy Thesaurus, Application Domain, Technology Topic, Popular Technical Reports.
© 2025 PatSnap. All rights reserved.Legal|Privacy policy|Modern Slavery Act Transparency Statement|Sitemap|About US| Contact US: help@patsnap.com