Manufacturing method of rotating shuttle plate
A manufacturing method and a technology of a rotary hook moon ring, which are applied in the field of sewing machine accessories, can solve the problems of complex structure, poor consistency of the rotary hook moon ring, large heat generation, etc., so as to overcome the low utilization rate, reduce production costs, and have good consistency. Effect
- Summary
- Abstract
- Description
- Claims
- Application Information
AI Technical Summary
Problems solved by technology
Method used
Examples
Embodiment 1
[0020] Embodiment 1 Manufacturing method of rotary shuttle moon ring
[0021] (1) Mix iron-nickel powder (Fe2%Ni0.2%C) with an organic binder (the amount of the organic binder is 9% of the weight of the iron-nickel powder), and then put the uniformly mixed material into the target moon circle In the shape of the mold;
[0022] (2) Injection molding to obtain the blank of the rotary shuttle moon circle; the injection temperature is 190°C, the pressure is 90MPa, and the mold temperature is 120°C;
[0023] (3) Catalyzed degreasing of the rotary shuttle moon ring blank to obtain a degreasing part; the degreasing temperature is 120°C, and the degreasing time is 2.5 hours;
[0024] (4) Sinter the degreased parts, wherein the sintering temperature is 1250-1300°C; the sintering adopts the gas protection sintering method, the sintering vacuum degree is 0.005MPa, and the sintering protection atmosphere is argon.
[0025] (5) After correcting the sintered part, the product of the rotar...
Embodiment 2
[0026] Embodiment 2 The manufacturing method of the rotary shuttle moon ring
[0027] (1) Mix iron-nickel powder (Fe2%Ni0.1%C) with an organic binder (the amount of the organic binder is 12% of the weight of the iron-nickel powder), and then put the uniformly mixed material into the target moon circle In the shape of the mold;
[0028] (2) Injection molding to obtain the blank of the rotary shuttle moon ring; the injection temperature is 180°C, the pressure is 100MPa, and the mold temperature is 115°C;
[0029] (3) Catalyzed degreasing of the rotary shuttle moon ring blank to obtain a degreasing part; the degreasing temperature is 115°C, and the degreasing time is 3 hours;
[0030] (4) Sinter the degreased parts, wherein the sintering temperature is 1250-1300°C; the sintering adopts the gas protection sintering method, the sintering vacuum degree is 0.01MPa, and the sintering protection atmosphere is helium.
[0031] (5) After correcting the sintered part, the product of the...
Embodiment 3
[0032] Embodiment 3 The manufacturing method of the rotary shuttle moon ring
[0033] (1) Mix iron-nickel powder (Fe2%Ni0.35%C) with an organic binder (the amount of the organic binder is 8% of the weight of the iron-nickel powder), and then put the uniformly mixed material into the target moon circle In the shape of the mold;
[0034] (2) Injection molding to obtain the blank of the rotary shuttle moon circle; the injection temperature is 200°C, the pressure is 80MPa, and the mold temperature is 125°C;
[0035] (3) Catalyzed degreasing of the rotary shuttle moon circle blank to obtain a degreasing part; the degreasing temperature is 125°C, and the degreasing time is 2 hours;
[0036] (4) Sinter the degreased parts, wherein the sintering temperature is 1250-1300°C; the sintering adopts the gas protection sintering method, the sintering vacuum is 0.008MPa, and the sintering protection atmosphere is argon.
[0037] (5) After correcting the sintered part, the product of the rot...
PUM
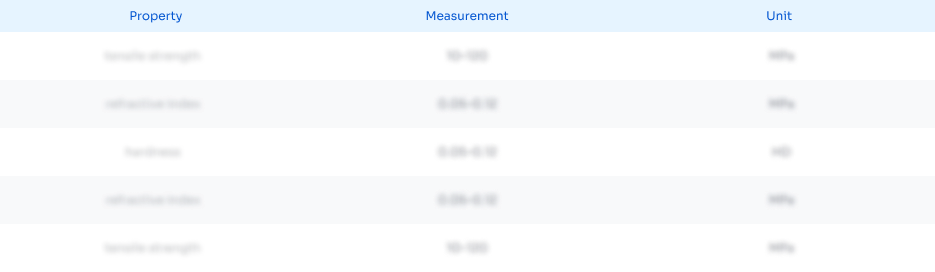
Abstract
Description
Claims
Application Information

- Generate Ideas
- Intellectual Property
- Life Sciences
- Materials
- Tech Scout
- Unparalleled Data Quality
- Higher Quality Content
- 60% Fewer Hallucinations
Browse by: Latest US Patents, China's latest patents, Technical Efficacy Thesaurus, Application Domain, Technology Topic, Popular Technical Reports.
© 2025 PatSnap. All rights reserved.Legal|Privacy policy|Modern Slavery Act Transparency Statement|Sitemap|About US| Contact US: help@patsnap.com