Preparation of high-temperature-resistant epoxy structural adhesive
A technology of epoxy structural adhesive and high temperature resistance, which is applied in the direction of epoxy resin glue, adhesive, non-polymer adhesive additives, etc., which can solve the problem of affecting product quality, overheating of epoxy adhesive and non-metallic bonding surface, and poor thermal conductivity and other issues, to achieve the effects of easy control, wide range of product uses, and low production costs
- Summary
- Abstract
- Description
- Claims
- Application Information
AI Technical Summary
Problems solved by technology
Method used
Examples
Embodiment 1
[0007] Epoxy resin E-51 50g, F-51 50g and toughening agent KH-07A 2.5g, KH-07B 2.5g, KH-07C 2.5g, KH-07D 2.5g, γ-aminopropyl triethoxy Add 1g of silane to the mixing kettle, stir at room temperature for 1h, and rotate at 100rpm; add 5g of alumina powder, 10g of spherical aluminum powder, and 5g of microsilica powder at 1000rpm for 20 minutes, mix well and reduce to room temperature, add 3g of dicyandiamide, 100A 1g, PN-23 1g, stir at 100rpm for 30min, and get out.
Embodiment 2
[0009] Epoxy resin E-51 50g, F-51 50g and toughening agent KH-07A 2.5g, KH-07B 2.5g, KH-07C 2.5g, KH-07D 2.5g, γ-aminopropyl triethoxy Add 1g of silane to the mixing kettle, stir at room temperature for 2h, and rotate at 180rpm; add 5g of alumina powder, 10g of spherical aluminum powder, 5g of microsilica powder, at 1200rpm, stir for 40min, mix well and reduce to room temperature, add 3g of dicyandiamide, 100A 1g, PN-23 1g, stir at 180rpm for 30min, and get it out.
Embodiment 3
[0011] Epoxy resin E-51 50g, F-51 50g and toughening agent KH-07A 2.5g, KH-07B 2.5g, KH-07C 2.5g, KH-07D 2.5g, γ-aminopropyl triethoxy Add 1g of silane to the mixing kettle, stir for 1.5h at room temperature, at a speed of 150rpm; add 5g of alumina powder, 10g of spherical aluminum powder, 5g of microsilica powder, at a speed of 1000rpm, stir for 30min, mix well and reduce to room temperature, add 3g of dicyandiamide, 100A 1g, PN-23 1g, stir at 120rpm for 30min, and get it out.
PUM
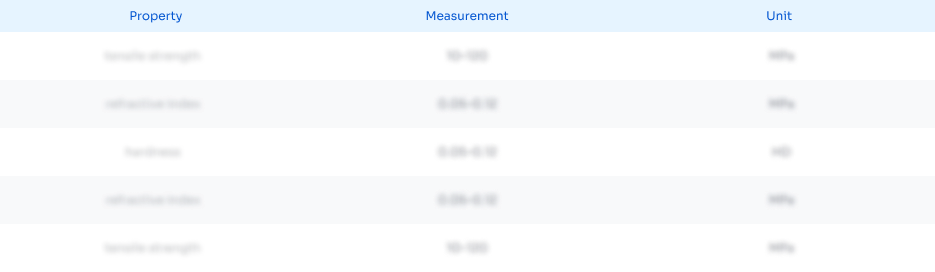
Abstract
Description
Claims
Application Information

- R&D
- Intellectual Property
- Life Sciences
- Materials
- Tech Scout
- Unparalleled Data Quality
- Higher Quality Content
- 60% Fewer Hallucinations
Browse by: Latest US Patents, China's latest patents, Technical Efficacy Thesaurus, Application Domain, Technology Topic, Popular Technical Reports.
© 2025 PatSnap. All rights reserved.Legal|Privacy policy|Modern Slavery Act Transparency Statement|Sitemap|About US| Contact US: help@patsnap.com