Method for modifying metal material surface through dielectric barrier discharge at atmospheric pressure and cold plasma jet
A dielectric barrier discharge and cold plasma technology, applied in the direction of plasma, metal material coating process, electrical components, etc., can solve the problems of difficult preparation, inability to change the surface structure, inconvenient for precise processing, etc., and achieve the concentration of modified areas. , the effect of high modification efficiency and simple operation
- Summary
- Abstract
- Description
- Claims
- Application Information
AI Technical Summary
Problems solved by technology
Method used
Image
Examples
Embodiment 1
[0035] Surface modification of superoleophobic aluminum sheet by atmospheric pressure dielectric barrier discharge cold plasma jet can significantly improve its surface energy and wettability, and realize the transformation from superoleophobic to superoleophilic. When the voltage is lower, its surface structure is not changed.
[0036] The cold plasma jet generator 4 adopts an insulated quartz glass tube, and the high-voltage electrode 5 is wound on 4 . The high-voltage power supply 6 adopts a sine wave AC power supply with an output frequency of 30-100 kHz and an output voltage of 0-30 kV; the high-voltage output end of the high-voltage power supply 6 is connected to the high-voltage electrode 5 on the cold plasma jet generator 4, and the low-voltage output end is grounded. The gas in the working gas source 1 is high-purity helium. After connecting the equipment, the distance between the outlet of the cold plasma jet generator 4 and the processed metal material 8 (aluminum-...
Embodiment 2
[0038] The surface modification of superoleophobic aluminum sheet was carried out by atmospheric pressure dielectric barrier discharge cold plasma jet to realize the transformation from superoleophobic to superoleophilic. When the voltage is higher, its surface structure can be changed to achieve long-term lyophilic modification.
[0039] The cold plasma jet generator 4 adopts an insulating PTFE (polytetrafluoroethylene) tube, and adopts the high-voltage power supply described in the specific embodiment 1. The connection mode of the jet generator and the high-voltage power supply is the same as that of the specific embodiment 1. Turn on the gas source processing device 2, adjust the gas mass flow controller 3 to make the helium flow reach 3SLM; turn on the high-voltage power supply 6, adjust the output frequency to 56kHz, and gradually increase the output voltage to 30kV. At this time, the dielectric barrier discharge cold plasma jet 7 acts on the surface of the superoleophobi...
Embodiment 3
[0041] Surface modification of superhydrophobic aluminum sheet by atmospheric pressure dielectric barrier discharge cold plasma jet can significantly improve its surface energy and wettability in a short time, and realize the rapid transformation from superhydrophobic to superhydrophilic.
[0042] The cold plasma jet generator 4 adopts an insulating alumina ceramic tube. The high-voltage power supply and its connection with the jet generator are the same as those in the specific embodiment 1, and the operation steps and methods are also the same. As shown in Figure 7, the water contact angle of the superhydrophobic aluminum surface before treatment is about 157°, and after only 1 s treatment, the contact angle becomes 20°, which is hydrophilic. After 3 s of treatment, the contact angle was 0°. It can be seen that this modification method can realize the rapid modification of superhydrophobic aluminum sheets.
PUM
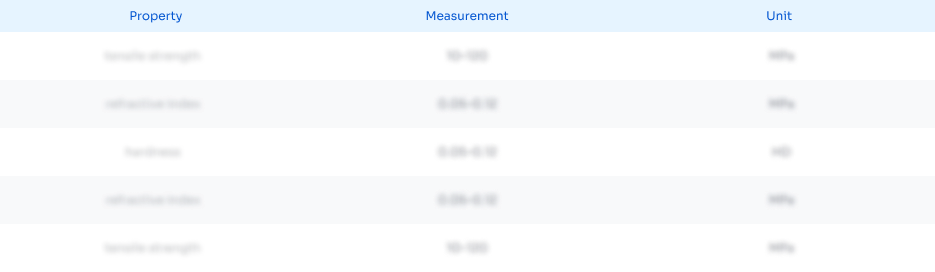
Abstract
Description
Claims
Application Information

- Generate Ideas
- Intellectual Property
- Life Sciences
- Materials
- Tech Scout
- Unparalleled Data Quality
- Higher Quality Content
- 60% Fewer Hallucinations
Browse by: Latest US Patents, China's latest patents, Technical Efficacy Thesaurus, Application Domain, Technology Topic, Popular Technical Reports.
© 2025 PatSnap. All rights reserved.Legal|Privacy policy|Modern Slavery Act Transparency Statement|Sitemap|About US| Contact US: help@patsnap.com