Selective recovery method of lithium in waste and old lithium iron phosphate batteries
A lithium iron phosphate battery, a selective technology, applied in the direction of battery recycling, waste collector recycling, recycling technology, etc., can solve the problems of reducing the grade of recycled products, high waste water treatment costs, and increasing recycling costs, so as to reduce recycling Cost, Simplified treatment process and difficulty of operation, Effect of reducing acid consumption
- Summary
- Abstract
- Description
- Claims
- Application Information
AI Technical Summary
Problems solved by technology
Method used
Image
Examples
Embodiment 1
[0048] (1) 100g of battery material powder containing aluminum, iron and lithium obtained by roasting and sorting waste batteries, by adding waste battery powder into NaOH alkali solution, the concentration of alkali solution is 3mol / L, to dissolve aluminum and aluminum oxides , to obtain iron-containing and lithium-containing residues.
[0049] (2) The obtained iron-containing lithium-containing residue is ball-milled to obtain iron-containing lithium-containing powder. The ball milling time is 2 hours, and the size of the iron-containing lithium-containing powder after ball milling is 500 mesh.
[0050] (3) The obtained iron-containing and lithium-containing powder is added to the 2 o 2 Auxiliary oxidation is carried out in an oxidizing medium to convert ferrous iron into ferric iron. The S / L ratio of the leaching slag phase solution is 100g / L, the mass ratio of mixed slag / oxidant is 20, and the oxidation treatment temperature is 25°C
[0051] . The stirring speed of th...
Embodiment 2
[0055] (1) 100g of battery material powder containing aluminum, iron, and lithium obtained by roasting and sorting waste batteries, by adding waste battery powder into KOH alkali solution with a concentration of 2mol / L to dissolve aluminum and aluminum oxides , to obtain iron-containing and lithium-containing residues.
[0056] (2) The obtained iron-containing lithium-containing residue is ball-milled to obtain iron-containing lithium-containing powder. The ball milling time is 2 hours, and the size of the iron-containing lithium-containing powder after ball milling is 500 mesh.
[0057] (3) The obtained iron-containing and lithium-containing powder contains MnO 2 Auxiliary oxidation in an oxidizing aqueous solution converts ferrous iron to ferric iron. The S / L ratio of the leaching slag phase solution is 100g / L, the mass ratio of mixed slag / oxidant is 20, and the oxidation treatment temperature is 25°C. The stirring speed of the oxidation treatment was 200 rpm.
[0058] (...
Embodiment 3
[0061] (1) 100g of battery material powder containing aluminum, iron, and lithium obtained by roasting and sorting waste batteries, by adding the waste battery powder into the ammonia alkali solution, the concentration of the alkali solution is 2mol / L, to dissolve aluminum and aluminum oxides , to obtain iron-containing and lithium-containing residues.
[0062] (2) The obtained iron-containing lithium-containing residue is ball-milled to obtain iron-containing lithium-containing powder. The ball milling time is 2 hours, and the size of the iron-containing lithium-containing powder after ball milling is 500 mesh.
[0063] (3) The obtained iron-containing lithium-containing powder is placed in an aqueous solution and oxidized by oxygen exposure to convert divalent iron into ferric iron. The S / L ratio of the leaching slag phase solution is 100g / L, the mixed slag / oxygen volume ratio is 0.1, the oxidation treatment temperature is 25°C, and the oxidation treatment stirring speed is...
PUM
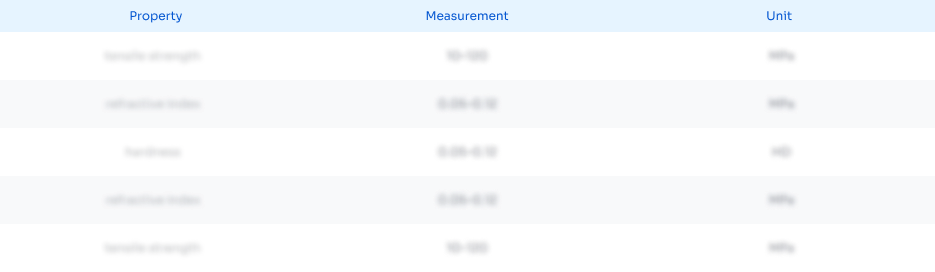
Abstract
Description
Claims
Application Information

- R&D
- Intellectual Property
- Life Sciences
- Materials
- Tech Scout
- Unparalleled Data Quality
- Higher Quality Content
- 60% Fewer Hallucinations
Browse by: Latest US Patents, China's latest patents, Technical Efficacy Thesaurus, Application Domain, Technology Topic, Popular Technical Reports.
© 2025 PatSnap. All rights reserved.Legal|Privacy policy|Modern Slavery Act Transparency Statement|Sitemap|About US| Contact US: help@patsnap.com