Method for preparing Fe2O3 nano-rod array electrodes by means of in-situ vulcanization and carbon coating and application of Fe2O3 nano-rod array electrodes
A nanorod array and carbon-coated technology, which is applied to battery electrodes, circuits, electrical components, etc., can solve the problems of loss of passivation, irreversible loss of sulfur ions, etc.
- Summary
- Abstract
- Description
- Claims
- Application Information
AI Technical Summary
Problems solved by technology
Method used
Image
Examples
Embodiment 1
[0027]The first step: Weigh 2.5mmol ferric chloride and dissolve it in 50mL deionized water, obtain a transparent solution under the action of ultrasound, then slowly add 2.5mmol sodium sulfate under magnetic stirring, and after it is completely dissolved, dissolve the solution Pour into a 50mL polytetrafluoroethylene liner. Put a 3cm×5cm titanium sheet into a polytetrafluoroethylene liner filled with the solution, seal it with a stainless steel jacket, put it in a constant temperature drying oven at 180°C, and keep it warm for 6h. After the reaction kettle was lowered to room temperature, the Ti sheet was taken out, the surface of the Ti sheet was washed repeatedly with deionized water, and dried under natural conditions, then put into a muffle furnace for sintering. From room temperature to 100°C, keep for 2h; within 3h, increase the temperature from 100°C to 300°C, and keep for 2h; within 3h, increase the temperature from 300°C to 450°C, and keep for 2h; naturally cool to g...
Embodiment 2
[0035] Compared with Example 1, except that the vulcanizing agent (thioacetamide 2mmol) in the second step is different, all the other are the same as Example 1
Embodiment 3
[0037] Compared with Example 1, except that vulcanizing agent (thioacetamide 5mmol) is different in the second step, all the other are the same as Example 1 Example 4
[0038] Compared with Example 1, except that the vulcanization time (1h) is different in the second step, all the other are the same as Example 1.
PUM
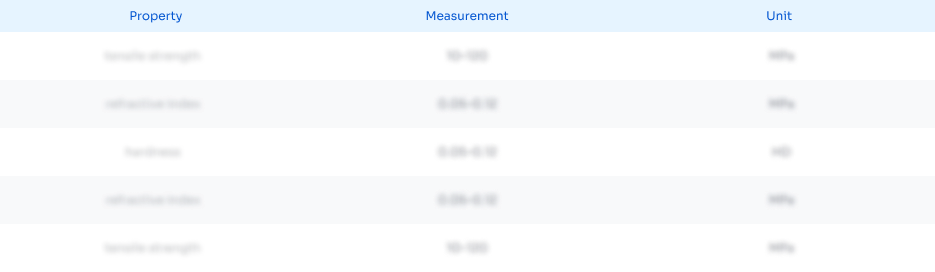
Abstract
Description
Claims
Application Information

- R&D Engineer
- R&D Manager
- IP Professional
- Industry Leading Data Capabilities
- Powerful AI technology
- Patent DNA Extraction
Browse by: Latest US Patents, China's latest patents, Technical Efficacy Thesaurus, Application Domain, Technology Topic, Popular Technical Reports.
© 2024 PatSnap. All rights reserved.Legal|Privacy policy|Modern Slavery Act Transparency Statement|Sitemap|About US| Contact US: help@patsnap.com