Method for Avoiding Singular Points in Five-Axis Machining Tool Trajectory
A singular point and trajectory technology, applied in the field of CNC machining, can solve the problems of low machining accuracy and loss of machining accuracy, and achieve the effect of small machining error, solving the loss of machining accuracy and small deformation.
- Summary
- Abstract
- Description
- Claims
- Application Information
AI Technical Summary
Problems solved by technology
Method used
Image
Examples
Embodiment Construction
[0039] refer to figure 1 . The specific steps of the method for avoiding the singular point of the five-axis machining tool path of the present invention are as follows:
[0040] (1) The structure of the CNC machine tool is selected as an AC cradle-type five-axis CNC machine tool, and the direction of the cutter axis provided in the following table includes a singular point, which is used to verify the optimality and validity of the solution obtained by the present invention.
[0041] o i
o j
o k
-0.21257
0.517408
0.828918
-0.10497
0.551995
0.827214
0.039348
0.552476
0.8326
0.174532
0.49917
0.848745
0.229676
0.450821
0.86256
0.241074
0.411043
0.879162
0.236042
0.368178
0.899294
0.220308
0.332003
0.917191
0.192137
0.298275
0.934941
0.113986
0.23168
0.966091
0.020798
0.128132
0.991539
-0.00434
0.085168
0.996357
-0...
PUM
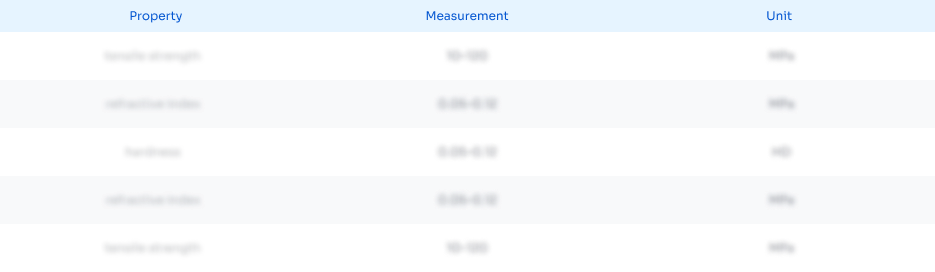
Abstract
Description
Claims
Application Information

- R&D
- Intellectual Property
- Life Sciences
- Materials
- Tech Scout
- Unparalleled Data Quality
- Higher Quality Content
- 60% Fewer Hallucinations
Browse by: Latest US Patents, China's latest patents, Technical Efficacy Thesaurus, Application Domain, Technology Topic, Popular Technical Reports.
© 2025 PatSnap. All rights reserved.Legal|Privacy policy|Modern Slavery Act Transparency Statement|Sitemap|About US| Contact US: help@patsnap.com