Stress whitening resistant low-temperature impact resistant polypropylene material and preparation method thereof
A technology of anti-stress whitening and polypropylene materials, which is applied in the field of modified polypropylene materials and its production, can solve the problems of unsatisfactory mechanical properties, poor low-temperature impact performance, and unsuitable parts, etc., to improve the bending stress Whitening performance, improved low temperature impact resistance, and wide applicability
- Summary
- Abstract
- Description
- Claims
- Application Information
AI Technical Summary
Problems solved by technology
Method used
Image
Examples
Embodiment 1
[0031] Weigh the components according to the following parts by weight: 10.0 parts of impact copolymerized polypropylene, 50.0 parts of random copolymerized polypropylene, 15.0 parts of ethylene-octene copolymer, 5.0 parts of high-density polyethylene, 20.0 parts of talcum powder, toner 1.0 part, 0.3 part of antioxidant 1010, 0.3 part of antioxidant 168, each component is placed in the high-speed mixer and fully stirred to obtain a premix, and the premix is added to the main feeding port of the twin-screw extruder , melt extrusion, granulation and drying to obtain stress-whitening and low-temperature impact-resistant polypropylene materials.
[0032] The melt extrusion conditions of the twin-screw extruder are: the temperature of the first zone is 80-120°C, the temperature of the second zone is 190-210°C, the temperature of the third zone is 210-230°C, the temperature of the fourth zone is 210-230°C, and the temperature of the fifth zone is 210- 230°C, the temperature in the...
Embodiment 2
[0034] Weigh the components according to the following parts by weight: 10.0 parts of impact copolymerized polypropylene, 60.0 parts of random copolymerized polypropylene, 10.0 parts of ethylene-octene copolymer, 5.0 parts of high-density polyethylene, 15.0 parts of talcum powder, toner 1.0 part, 0.3 part of antioxidant 1010, 0.3 part of antioxidant 168, each component is placed in the high-speed mixer and fully stirred to obtain a premix, and the premix is added to the main feeding port of the twin-screw extruder , melt extrusion, granulation and drying to obtain stress-whitening and low-temperature impact-resistant polypropylene materials.
[0035] The melt extrusion conditions of the twin-screw extruder are: the temperature of the first zone is 80-120°C, the temperature of the second zone is 190-210°C, the temperature of the third zone is 210-230°C, the temperature of the fourth zone is 210-230°C, and the temperature of the fifth zone is 210- 230°C, the temperature in the...
Embodiment 3
[0037] Weigh the components according to the following parts by weight: 10.0 parts of impact copolymerized polypropylene, 60.0 parts of random copolymerized polypropylene, 10.0 parts of ethylene-octene copolymer, 10.0 parts of high-density polyethylene, 10.0 parts of talcum powder, toner 1.0 part, 0.3 part of antioxidant 1010, 0.3 part of antioxidant 168, each component is placed in the high-speed mixer and fully stirred to obtain a premix, and the premix is added to the main feeding port of the twin-screw extruder , melt extrusion, granulation and drying to obtain stress-whitening and low-temperature impact-resistant polypropylene materials.
[0038] The melt extrusion conditions of the twin-screw extruder are: the temperature of the first zone is 80-120°C, the temperature of the second zone is 190-210°C, the temperature of the third zone is 210-230°C, the temperature of the fourth zone is 210-230°C, and the temperature of the fifth zone is 210- 230°C, the temperature in th...
PUM
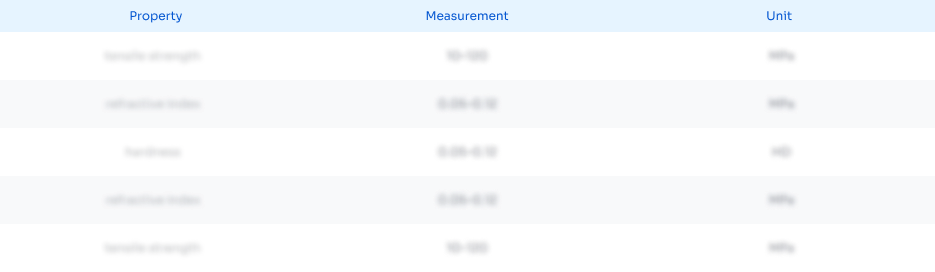
Abstract
Description
Claims
Application Information

- R&D Engineer
- R&D Manager
- IP Professional
- Industry Leading Data Capabilities
- Powerful AI technology
- Patent DNA Extraction
Browse by: Latest US Patents, China's latest patents, Technical Efficacy Thesaurus, Application Domain, Technology Topic, Popular Technical Reports.
© 2024 PatSnap. All rights reserved.Legal|Privacy policy|Modern Slavery Act Transparency Statement|Sitemap|About US| Contact US: help@patsnap.com