Method for producing low-manganese steel
A low-manganese steel and molten steel technology applied in the field of metallurgy to achieve the effects of easy operation, high cost and reasonable process time
- Summary
- Abstract
- Description
- Claims
- Application Information
AI Technical Summary
Problems solved by technology
Method used
Examples
Embodiment 1
[0015] A method for producing low manganese steel, the specific steps are as follows:
[0016] (1) Mix the desulfurized molten iron into the 1# converter with a capacity of 100t. Add about 3 tons of lime within 3 minutes of the start of smelting, and add the remaining 1 ton of lime at 4 minutes. The gun position is controlled at 2.2m~2.4m in the first 4 minutes, and the oxygen flow rate is controlled at 20000m 3 / h about, oxygen pressure 0.75 ~ 0.85MPa;
[0017] (2) The tapping temperature of the first half of the steel is 1438°C, the slag is blocked and the slag thickness is 70mm. The molten iron composition and the first half steel tapping composition are shown in Table 1:
[0018] Table 1 Tapping composition of molten iron and 1# converter (wt%)
[0019] C Si mn P S molten iron 4.45 0.52 0.16 0.10 0.005 Converter tapping 2.8 0.012 0.05 0.039 0.009
[0020] (3) The second half of the steel is operated in the 2# furnace. According ...
Embodiment 2
[0028] A method for producing low manganese steel, the specific steps are as follows:
[0029] (1) Mix the desulfurized molten iron into the 1# converter with a capacity of 100t. Add about 3 tons of lime within 3 minutes of the start of smelting, and add the remaining 1 ton of lime at 4 minutes. The gun position is controlled at 2.2m~2.4m in the first 4 minutes, and the oxygen flow rate is controlled at 20000m 3 / h about, oxygen pressure 0.75 ~ 0.85MPa;
[0030] (2) The tapping temperature of the first half of the steel is 1422°C, the slag is blocked and the slag thickness is 70mm. The molten iron composition and the first half steel tapping composition are shown in Table 4:
[0031] Table 4 Tapping composition of molten iron and 1# converter (wt%)
[0032] C Si mn P S molten iron 4.45 0.47 0.19 0.08 0.005 Converter tapping 2.85 0.01 0.054 0.028 0.010
[0033] (3) The second half of the steel is operated in the 2# furnace. According...
Embodiment 3
[0041] A method for producing low manganese steel, the specific steps are as follows:
[0042] (1) Mix the desulfurized molten iron into the 1# converter with a capacity of 100t. Add about 3 tons of lime within 3 minutes of the start of smelting, and add the remaining 1 ton of lime at 4 minutes. The gun position is controlled at 2.2m~2.4m in the first 4 minutes, and the oxygen flow rate is controlled at 20000m 3 / h about, oxygen pressure 0.75 ~ 0.85MPa;
[0043] (2) The tapping temperature of the first half of the steel is 1432°C, the slag is blocked and the slag thickness is 70mm. The molten iron composition and the first half steel tapping composition are shown in Table 7:
[0044] Table 7 Tapping composition of molten iron and 1# converter (wt%)
[0045] C Si mn P S molten iron 4.47 0.33 0.22 0.077 0.0048 Converter tapping 2.81 0.011 0.05 0.034 0.009
[0046] (3) The second half of the steel is operated in the 2# furnace. Accordi...
PUM
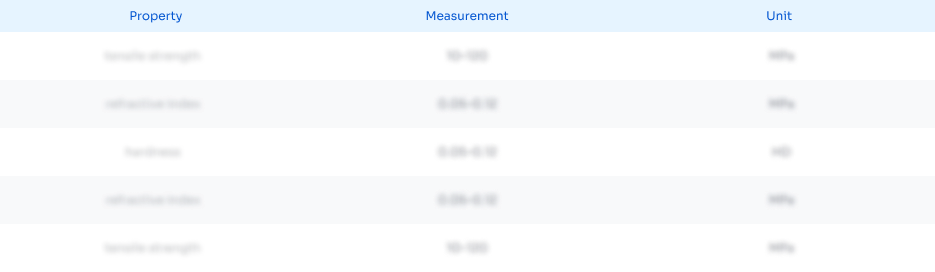
Abstract
Description
Claims
Application Information

- Generate Ideas
- Intellectual Property
- Life Sciences
- Materials
- Tech Scout
- Unparalleled Data Quality
- Higher Quality Content
- 60% Fewer Hallucinations
Browse by: Latest US Patents, China's latest patents, Technical Efficacy Thesaurus, Application Domain, Technology Topic, Popular Technical Reports.
© 2025 PatSnap. All rights reserved.Legal|Privacy policy|Modern Slavery Act Transparency Statement|Sitemap|About US| Contact US: help@patsnap.com