Method for improving sulfuration resistant and UV resistant performances of organosilicon material for LED packaging
An LED packaging and silicone technology, applied in coatings, electrical components, circuits, etc., can solve the problems of poor high and low temperature resistance, poor aging resistance, blackening of silver layer, etc., and achieve good adhesion and vulcanization resistance. good effect
- Summary
- Abstract
- Description
- Claims
- Application Information
AI Technical Summary
Problems solved by technology
Method used
Image
Examples
Embodiment 1
[0023] A method for improving the sulfuration-resistant and UV-resistant performance of organic silicon materials for LED packaging, comprising the steps of:
[0024] 1) Clean the surface of the LED bracket;
[0025] 2) Prepare the coating: uniformly mix 25 parts of hydrogen-containing silicone resin and 75 parts of solvent anhydrous ether to obtain a coating;
[0026] 3) uniformly spray the coating obtained in step 2) onto the surface of the chip;
[0027] 4) Uniform electron beam irradiation is carried out to the chip surface obtained in step 3), the electron beam is 500mW, and the irradiation time is 5 seconds, so that the coating is cured to form a dense silicon dioxide structure;
[0028] 5) Finally, remove the excess coating, apply the silicone material for encapsulation, and cure and shape.
Embodiment 2
[0030] A method for improving the sulfuration-resistant and UV-resistant performance of organic silicon materials for LED packaging, comprising the steps of:
[0031] 1) Clean the surface of the LED bracket;
[0032] 2) Prepare the coating: uniformly mix 23 parts of hydrogen-containing silicone resin and 77 parts of solvent anhydrous n-heptane to obtain a coating;
[0033] 3) uniformly spray the coating obtained in step 2) onto the surface of the chip;
[0034] 4) Uniform electron beam irradiation is carried out to the chip surface obtained in step 3), the electron beam is 700mW, and the irradiation time is 4 seconds, so that the coating is cured to form a dense silicon dioxide structure;
[0035] 5) Finally, remove the excess coating, apply the silicone material for encapsulation, and cure and shape.
Embodiment 3
[0037] A method for improving the sulfuration-resistant and UV-resistant performance of organic silicon materials for LED packaging, comprising the steps of:
[0038] 1) Clean the surface of the LED bracket;
[0039] 2) Prepare the coating: uniformly mix 20 parts of hydrogen-containing silicone resin and 80 parts of solvent anhydrous acetone to obtain a coating;
[0040] 3) uniformly spray the coating obtained in step 2) onto the surface of the chip;
[0041] 4) Uniform electron beam irradiation is carried out to the chip surface obtained in step 3), the electron beam is 1000mW, and the irradiation time is 3 seconds, so that the coating is cured to form a dense silicon dioxide structure;
[0042] 5) Finally, remove the excess coating, apply the silicone material for encapsulation, and cure and shape.
PUM
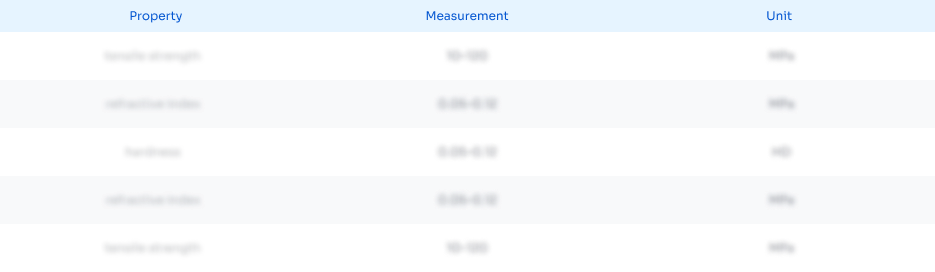
Abstract
Description
Claims
Application Information

- Generate Ideas
- Intellectual Property
- Life Sciences
- Materials
- Tech Scout
- Unparalleled Data Quality
- Higher Quality Content
- 60% Fewer Hallucinations
Browse by: Latest US Patents, China's latest patents, Technical Efficacy Thesaurus, Application Domain, Technology Topic, Popular Technical Reports.
© 2025 PatSnap. All rights reserved.Legal|Privacy policy|Modern Slavery Act Transparency Statement|Sitemap|About US| Contact US: help@patsnap.com