Loaded angle radial logarithmic zigzag line micro-strip slow-wave structure based on photonic band gap structure
A slow-wave structure, photonic bandgap technology, which is applied to the circuit components of transit-time electron tubes and other directions, can solve the problems of increased process cost, reduced efficiency of traveling wave tube, and reduced performance and stability, and achieves increased process cost, The effect of increasing output power and reducing complexity
- Summary
- Abstract
- Description
- Claims
- Application Information
AI Technical Summary
Problems solved by technology
Method used
Image
Examples
Embodiment 1
[0054]w is the width of the angle radial logarithmic microstrip meander, θ is the angular angle of the angle radial logarithmic microstrip meander, r is the initial radius of the logarithmic helix of the angle radial logarithmic microstrip meander, l_sws is the radial length of the angle radial logarithmic microstrip zigzag line, c_sws is the 45° chamfer length of the right angle bending of the angle radial logarithmic microstrip zigzag line, d_lr is the angle radial logarithmic microstrip zigzag line The length of the extended section at the input and output terminals, n is the number of cycles.
[0055] p is the width of the microstrip line constituting the photonic bandgap structure pattern, p1 is the side length of the square photonic bandgap structure, and p2 is the length of the local square pattern of the photonic bandgap structure.
[0056] rc is the radius of the top of the side microstrip line and the arc at both ends, θc is the angle of the hypotenuse of the side mi...
PUM
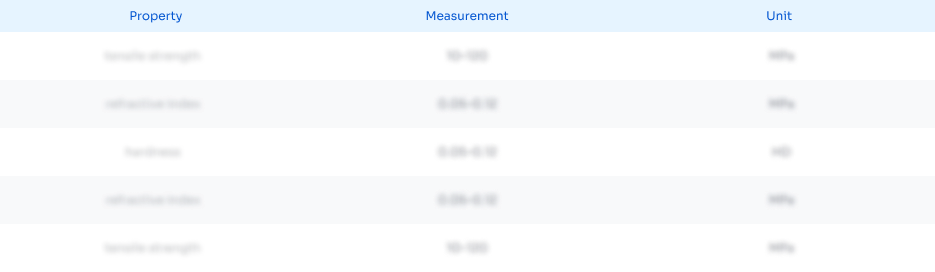
Abstract
Description
Claims
Application Information

- R&D
- Intellectual Property
- Life Sciences
- Materials
- Tech Scout
- Unparalleled Data Quality
- Higher Quality Content
- 60% Fewer Hallucinations
Browse by: Latest US Patents, China's latest patents, Technical Efficacy Thesaurus, Application Domain, Technology Topic, Popular Technical Reports.
© 2025 PatSnap. All rights reserved.Legal|Privacy policy|Modern Slavery Act Transparency Statement|Sitemap|About US| Contact US: help@patsnap.com