Making process of high-fastness polyamide-polyester interwoven fabric
A production process and fastness technology, which is applied in the production process of high-fastness nylon-polyester interwoven fabrics, can solve the problems of fastness that plagues textile workers and other problems, and achieve the effects of reducing the risk of fading, good color fastness and fashionable appearance.
- Summary
- Abstract
- Description
- Claims
- Application Information
AI Technical Summary
Problems solved by technology
Method used
Examples
Embodiment 1
[0021] Step 1 Yarn material selection: choose nylon 6 fully drawn yarn 40D / 34F for the warp yarn, choose modified polyester false twist textured yarn 50D / 72F for the weft yarn, and the number of warp yarns is 1100 grains; among them, choose nylon 6 fiber of 70D or below for the warp yarn: its It belongs to nylon fully stretched filament, this kind of yarn has good bulkiness, soft and comfortable hand feeling; the weft yarn chooses 75D and below modified polyester fiber: it is a cationic dye-dyeable polyester fiber, that is, CDP fiber; due to the use of ion modified It not only greatly improves the color absorption performance of the fiber, but also reduces the crystallinity so that the dye molecules are easy to penetrate, making the fiber easy to dye, and the color absorption rate is improved; this kind of fiber not only ensures the easy dyeing of cations, but also increases the micro It is cationic dyeable polyester fiber; this kind of yarn material has uniform color dyeing ra...
Embodiment 2
[0032] Step 1 Yarn material selection: warp yarn selection nylon 6 fully drawn yarn 20D / 24F, weft yarn selection
[0033] Modified polyester fully drawn yarn 40D / 24F, the number of warp yarns is 1344 grains;
[0034] Step 2 Warping in batches: at a speed of 300m / min, the nylon 6 fully drawn yarn is assembled into a whole shaft by a batch warping machine, and a total of 10 whole shafts need to be made;
[0035] Step 3 Sizing: at a speed of 100m / min, the yarn is sizing through a sizing machine; the water-jet loom adopts acrylic sizing, the sizing concentration of the yarn is controlled at 13%, and the sizing temperature is controlled at 45°C. The slurry is HW-132 slurry from Jiangyin Haohe;
[0036] Step 4 paralleling: at a speed of 40m / min, combine the entire beams in step 2 into one weaving beam through a paralleling machine;
[0037] Step 5 Weaving: at a speed of 500rpm, hang the weft modified polyester fully drawn yarn 40D / 24F on the weft frame, and through the back and fo...
Embodiment 3
[0044] Step 1 Yarn material selection: warp yarn selection nylon 6 fully stretched yarn 70D / 48F, weft yarn selection
[0045] Modified polyester false twist textured yarn 75D / 72F, the number of warp yarns is 1008 grains;
[0046] Step 2 Warping in batches: At a speed of 450m / min, the nylon 6 fully drawn yarn is assembled into an entire shaft by a batch warping machine, and a total of 8 entire shafts are required;
[0047] Step 3 Sizing: At a speed of 120m / min, the yarn is sizing through a sizing machine; the water-jet loom adopts acrylic sizing, the sizing concentration of the yarn is controlled at 11%, and the sizing temperature is controlled at 45°C. The slurry is WJ-88 slurry from Jiangyin Haohe;
[0048] Step 4 paralleling: at a speed of 120m / min, combine the entire beams in step 2 into one weaving beam through a paralleling machine;
[0049] Step 5 Weaving: At a speed of 550rpm, hang the weft yarn modified polyester false twisted textured yarn 50D / 72F on the weft creel,...
PUM
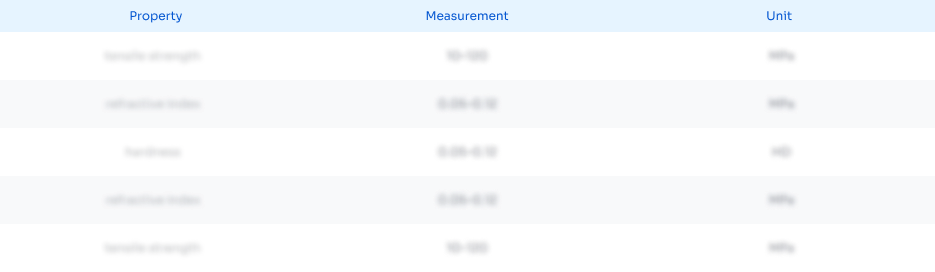
Abstract
Description
Claims
Application Information

- R&D
- Intellectual Property
- Life Sciences
- Materials
- Tech Scout
- Unparalleled Data Quality
- Higher Quality Content
- 60% Fewer Hallucinations
Browse by: Latest US Patents, China's latest patents, Technical Efficacy Thesaurus, Application Domain, Technology Topic, Popular Technical Reports.
© 2025 PatSnap. All rights reserved.Legal|Privacy policy|Modern Slavery Act Transparency Statement|Sitemap|About US| Contact US: help@patsnap.com