Ferroalumen slag cold-bonded and reduced pellet preparation and recycled lead, zinc and iron synchronous sulfur fixation process method
A process method, the technology of jarosite slag, which is applied in the field of preparation of cold-consolidated reduction pellets of jarosite slag and its recovery of lead, zinc and iron synchronous sulfur fixation, which can solve the problems of large amount of chemicals, pollution of the environment by sulfur volatilization, and low roasting efficiency. problems, achieve efficient and clean utilization, avoid sulfur emissions, and achieve good roasting effects
- Summary
- Abstract
- Description
- Claims
- Application Information
AI Technical Summary
Problems solved by technology
Method used
Image
Examples
Embodiment 1
[0037] Alumite slag contains Pb, Zn, Fe, S, H 2 O is 3.01%, 6.95%, 26.76%, 10.16%, and 35%, respectively. When the mass ratio of iron slag, lignite, and CaO is 100:25:27.5, the balling pressure is 12MPa, the balls are formed at 150°C for 10 minutes, and the balls are directly dried at 1250°C. Under the condition of reduction for 60 minutes, the volatilization rate of Pb and Zn were 96.97% and 99.89%, the rate of sulfur fixation was 98.91%, and the metallization rate of iron was 91.97%. The calcined sand adopts two-stage grinding and two-stage magnetic separation processes. The first-stage grinding fineness -74μm accounts for 95.97%, the first-stage magnetic field strength is 199.04kA / m, the second-stage grinding fineness-30μm accounts for 93.46%, and the second-stage magnetic field strength is 31.85kA / m Under the optimal conditions, iron concentrates with iron grades and recovery rates of 74.6% and 59.66% can be obtained, and iron concentrates contain 0.38% sulfur. Tailings ...
Embodiment 2
[0039] Alumite slag contains Pb, Zn, Fe, S, H 2 O is 3.01%, 6.95%, 26.76%, 10.16%, and 30%, respectively. When the mass ratio of alum slag, lignite, and CaO is 100:20:25, the balling pressure is 15MPa, the balls are dried at 150°C for 10 minutes, and the balls are directly Under the condition of reduction for 120min, the volatilization rate of Pb and Zn were 96.48% and 99.88%, the rate of sulfur fixation was 93.29%, and the metallization rate of iron was 82.59%. The calcined sand adopts two-stage grinding and two-stage magnetic separation processes. The first-stage grinding fineness -74μm accounts for 92.45%, the first-stage magnetic field strength is 199.04kA / m, the second-stage grinding fineness-30μm accounts for 93.53%, and the second-stage magnetic field strength is 31.85kA / m Under the optimal conditions, iron concentrates with iron grades and recovery rates of 72.0% and 57.10% can be obtained, and iron concentrates contain 0.36% sulfur. The tailings contain 18.13% and 2...
Embodiment 3
[0042] Alumite slag contains Pb, Zn, Fe, S, H 2 O is 3.01%, 6.95%, 26.76%, 10.16%, and 40%, respectively, when the mass ratio of alumina slag, coking coal, and CaO is 100:25:27.5, the balling pressure is 15MPa, the balls are formed at 150°C for 10 minutes, and the balls are directly dried at 1250°C. Under the condition of reduction for 120min, the volatilization rate of Pb and Zn were 96.87% and 99.95%, the rate of sulfur fixation was 97.40%, and the metallization rate of iron was 91.63%. The calcined sand adopts two-stage grinding and two-stage magnetic separation processes. The first-stage grinding fineness -74μm accounts for 90.35%, the first-stage magnetic field strength is 199.04kA / m, the second-stage grinding fineness-30μm accounts for 93.53%, and the second-stage magnetic field strength is 31.85kA / m Under the optimal conditions, iron concentrates with iron grades and recovery rates of 73.4% and 60.50% can be obtained, and iron concentrates contain 0.45% sulfur. Tailings...
PUM
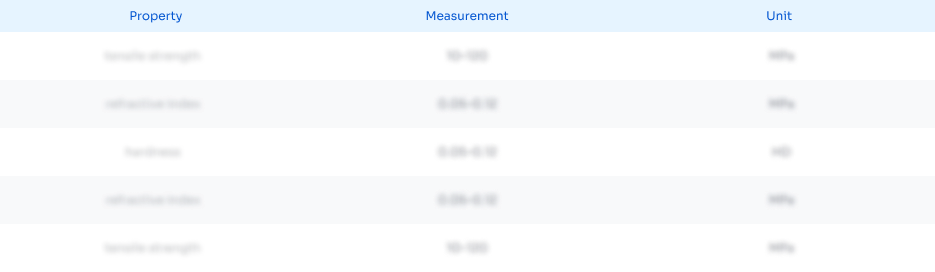
Abstract
Description
Claims
Application Information

- R&D
- Intellectual Property
- Life Sciences
- Materials
- Tech Scout
- Unparalleled Data Quality
- Higher Quality Content
- 60% Fewer Hallucinations
Browse by: Latest US Patents, China's latest patents, Technical Efficacy Thesaurus, Application Domain, Technology Topic, Popular Technical Reports.
© 2025 PatSnap. All rights reserved.Legal|Privacy policy|Modern Slavery Act Transparency Statement|Sitemap|About US| Contact US: help@patsnap.com