Method for removing blast furnace shaft wall accretion
A blast furnace and thickening technology, applied in blast furnace, blast furnace details, blast furnace parts and other directions, can solve the problems of difficult to grasp the amount of net coke just right, affecting the life of the blast furnace, unreliable effect, etc., to achieve easy and accurate adjustment and cleaning Reliable slag skin, loss reduction effect
- Summary
- Abstract
- Description
- Claims
- Application Information
AI Technical Summary
Problems solved by technology
Method used
Examples
Embodiment 1
[0018] Blast furnace (effective volume 3200m 3 ) The thickness of the furnace body junction is 557mm, and the cleaning steps are:
[0019] 1) Properly develop two airflows first, reduce the ore at the edge and the center by one ring each, and reduce the coke load, add 500kg of coke to each batch of material, increase the furnace temperature ([si] content) to about 0.6%, and reduce the slag The alkalinity is reduced from 1.20 to about 1.10, and 600kg of manganese ore is added to each batch of ore;
[0020] 2) When the furnace temperature reaches about 0.6%, start loading 120t net coke, and adjust the coke load to 2.7, and calculate the number of batches that need to be loaded according to the position of the root of the slag bark;
[0021] 3) Stop feeding and carry out empty material line operations: try to maintain a large air volume and stop coal injection (N2 from the coal gun does not stop); control the amount of water sprinkled on the furnace top so that the temperature o...
Embodiment 2
[0026] Blast furnace (effective volume 3200m 3 ) The average thickness of the furnace body is 476mm, and the processing steps are:
[0027] 1) Properly develop two airflows first, reduce the ore at the edge by one ring, and reduce the coke in the center by one ring (because the air volume is too small after the knot is thick, the center of the material surface is higher, and the dead coke column is larger), and the coke is lightened Load, add 500kg of coke to each batch of materials, increase the furnace temperature ([si] content) to about 0.6%, reduce the slag alkalinity from 1.21 to about 1.10, and add 600kg of manganese ore to each batch of ore;
[0028] 2) When the furnace temperature reaches about 0.6%, start loading 100t of clean coke, and adjust the coke load to 2.7, and calculate the number of batches that need to be loaded according to the position of the root of the slag bark;
[0029] 3) Stop feeding and carry out empty material line operations: try to maintain a l...
Embodiment 3
[0034] Blast furnace (effective volume 2600m 3 ) The average thickness of the furnace body is 340mm (the local thickest part is 460mm), and the processing steps are:
[0035] 1) Properly develop two airflows first, cancel the ore at the No. 9 corner of the edge (that is, only coke is placed at the No. 9 corner), and reduce one ring of coke in the center (because the air volume is too small after the knot is thick, the center of the material surface is higher, and the dead The coke column is relatively large), and the coke load is lightened. Add 400kg of coke to each batch of materials to increase the furnace temperature ([si] content) to about 0.6%, and reduce the slag alkalinity from 1.20 to about 1.10. Add 500kg manganese ore;
[0036] 2) When the furnace temperature reaches about 0.6%, start loading 80t of clean coke, and adjust the coke load to 2.7, and calculate the number of batches that need to be loaded according to the position of the root of the slag bark;
[0037]...
PUM
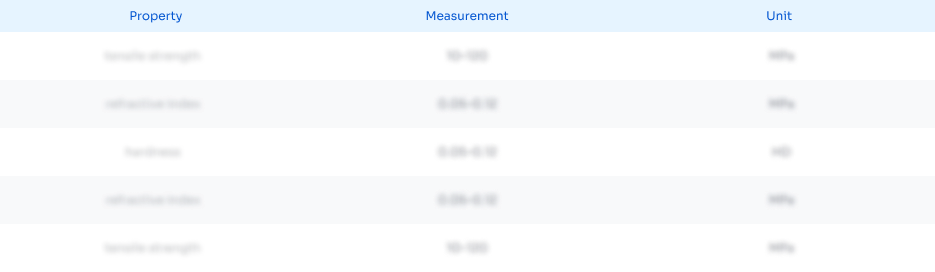
Abstract
Description
Claims
Application Information

- Generate Ideas
- Intellectual Property
- Life Sciences
- Materials
- Tech Scout
- Unparalleled Data Quality
- Higher Quality Content
- 60% Fewer Hallucinations
Browse by: Latest US Patents, China's latest patents, Technical Efficacy Thesaurus, Application Domain, Technology Topic, Popular Technical Reports.
© 2025 PatSnap. All rights reserved.Legal|Privacy policy|Modern Slavery Act Transparency Statement|Sitemap|About US| Contact US: help@patsnap.com