Polyurethane damping material and preparation method thereof
A shock-absorbing material, polyurethane technology, applied in the field of shock-absorbing materials, can solve the problems of limited use temperature range, unsuitable for high-temperature use, limited shock-absorbing performance, etc. Effect
- Summary
- Abstract
- Description
- Claims
- Application Information
AI Technical Summary
Problems solved by technology
Method used
Image
Examples
preparation example Construction
[0024] Such as figure 1 Shown, the preparation method of the polyurethane shock-absorbing material of one embodiment, comprises the following steps:
[0025] S10, kneading the polyurethane elastomer to obtain a kneaded polyurethane elastomer.
[0026] Wherein, in the step of kneading the polyurethane elastomer, the kneading temperature may be 180° C. to 210° C., and the kneading time may be 3 min to 10 min.
[0027] S20, uniformly mixing the shear thickening gel and the compatibilizer to obtain a uniformly mixed shear thickening gel and the compatibilizer.
[0028] Among them, the compatibilizer can be polydimethylsiloxane-polyethylene glycol, polyglycidyl ester, divinyl tetramethyl disiloxane, vinyl triethoxy siloxane, vinyl trichloro Silane, vinyltris(β-methoxyethoxy)silane, γ-glycidylpropyl-trimethoxysilane, γ-methacryloxypropyl-trimethoxysilane, N-(β-ammonia Ethyl)-γ-aminopropyl-methyl-trimethoxysilane, γ-chloropropyl-trimethoxysilane, γ-mercaptopropyl-trimethoxysilane,...
Embodiment 1
[0043] The polyurethane elastomer was kneaded, the kneading temperature was 190° C., and the kneading time was 5 min, to obtain the kneaded polyurethane elastomer.
[0044]Next, 100 parts of the shear thickening gel and 0.1 part of polydimethylsiloxane-polyethylene glycol were mixed on an open mixer, the mixing temperature was 100° C., and the mixing time was 2 minutes.
[0045] Add 20 parts of shear thickening gel and compatibilizer that have been mixed evenly to 100 parts of polyurethane elastomer that has been kneaded, and continue kneading. The kneading temperature is 190° C., and the kneading time is 6 minutes. After mixing evenly, add the vulcanizing agent DCP, and then mix for a period of time to produce tablets. After 24 hours, place the rubber on a flat vulcanizing agent for vulcanization at a temperature of 190°C and a pressure of 10 MPa for 7 minutes. That is, the final sample is obtained.
Embodiment 2
[0047] The polyurethane elastomer was kneaded, the kneading temperature was 200° C., and the kneading time was 3 minutes to obtain the kneaded polyurethane elastomer.
[0048] Next, 100 parts of the shear thickening gel and 0.5 part of divinyltetramethyldisiloxane were mixed on an open mixer, the mixing temperature was 80° C., and the mixing time was 5 minutes.
[0049] Add 20 parts of shear thickening gel and compatibilizer that have been mixed evenly to 100 parts of polyurethane elastomer that has been kneaded, and continue kneading. The kneading temperature is 180° C., and the kneading time is 8 min. Next, the uniformly mixed product is extruded and granulated on an extruder. Then the pellets were injection-molded on an injection molding machine, the nozzle temperature was 190°C, the injection pressure was 50MPa, the holding time was 60s, and the mold temperature was 50°C to obtain the final product.
PUM
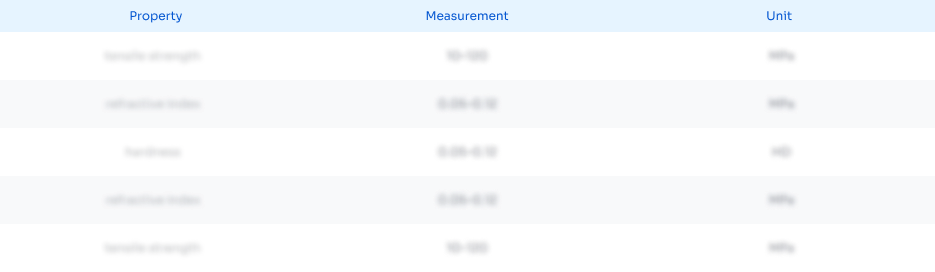
Abstract
Description
Claims
Application Information

- R&D
- Intellectual Property
- Life Sciences
- Materials
- Tech Scout
- Unparalleled Data Quality
- Higher Quality Content
- 60% Fewer Hallucinations
Browse by: Latest US Patents, China's latest patents, Technical Efficacy Thesaurus, Application Domain, Technology Topic, Popular Technical Reports.
© 2025 PatSnap. All rights reserved.Legal|Privacy policy|Modern Slavery Act Transparency Statement|Sitemap|About US| Contact US: help@patsnap.com