Active carbon prepared from wastes and method thereof
A technology of activated carbon and waste, applied in the field of activated carbon preparation, can solve the problems of easy collapse of activated carbon structure, increase the cost of activated carbon, affect adsorption effect, etc.
- Summary
- Abstract
- Description
- Claims
- Application Information
AI Technical Summary
Problems solved by technology
Method used
Examples
Embodiment 1
[0024] S1: 10 parts of waste ceramic sheets, 15 parts of waste tire rubber and 6 parts of cinder are dried and pulverized to granular, 200-300 mesh;
[0025] S2: add 3 parts of dimethicone, 10 parts of mercaptosuccinic acid, and 8 parts of resorcinol diglycidyl ether to the material obtained in step S1, heat up to 70°C, and stir for 20min at a rate of 600r / min;
[0026] S3: then add 7 parts of ethoxy amidobenzyl methyl ester and 6 parts of isoamyl salicylate to step S2, continue to heat up to 100 ° C, and stir for 15 min at a rate of 800 r / min;
[0027] S4; then add 10 parts of 1,4-cyclohexanedimethanol and 3 parts of dipotassium 2-naphthol-6,8-disulfonate to step S3, and soak for 2h;
[0028] S5: the product obtained in step S4 is heated to a carbonization temperature of 400° C. in a muffle furnace, and the reaction is maintained for 30 minutes; the activated carbon can be obtained after cooling, washing, filtering and drying.
Embodiment 2
[0035] S1: 15 parts of waste ceramic sheets, 10 parts of waste tire rubber and 10 parts of cinder are dried and pulverized to granular, 200-300 mesh;
[0036] S2: adding 7 parts of dimethicone, 15 parts of mercaptosuccinic acid, and 12 parts of resorcinol diglycidyl ether to the material obtained in step S1, heating to 90° C., stirring and reacting at a rate of 800 r / min for 25 min;
[0037] S3: then add 10 parts of ethoxybenzamide and 12 parts of isoamyl salicylate to step S2, continue to heat up to 120 ° C, and stir for 25 min at a rate of 1000 r / min;
[0038] S4; then add 16 parts of 1,4-cyclohexanedimethanol and 6 parts of dipotassium 2-naphthol-6,8-disulfonate to step S3, and soak for 4h;
[0039] S5: the product obtained in step S4 is heated to a carbonization temperature of 600° C. in a muffle furnace, and the reaction is maintained for 50 minutes; the activated carbon can be obtained after cooling, washing, filtering and drying.
Embodiment 3
[0046] S1: 12 parts of waste ceramic sheets, 11 parts of waste tire rubber and 8 parts of cinder are dried and pulverized to granular, 200-300 mesh;
[0047] S2: add 4 parts of dimethicone, 11 parts of mercaptosuccinic acid, and 9 parts of resorcinol diglycidyl ether to the material obtained in step S1, heat up to 70°C, and stir and react at a rate of 600r / min for 20min;
[0048] S3: then add 7 parts of ethoxynil and 8 parts of isoamyl salicylate to step S2, continue to heat up to 110 ° C, and stir for 25 min at a rate of 1000 r / min;
[0049] S4; then add 12 parts of 1,4-cyclohexanedimethanol and 4 parts of dipotassium 2-naphthol-6,8-disulfonate to step S3, and soak for 2h;
[0050] S5: the product obtained in step S4 is heated to a carbonization temperature of 400° C. in a muffle furnace, and the reaction is maintained for 30 minutes; the activated carbon can be obtained after cooling, washing, filtering and drying.
PUM
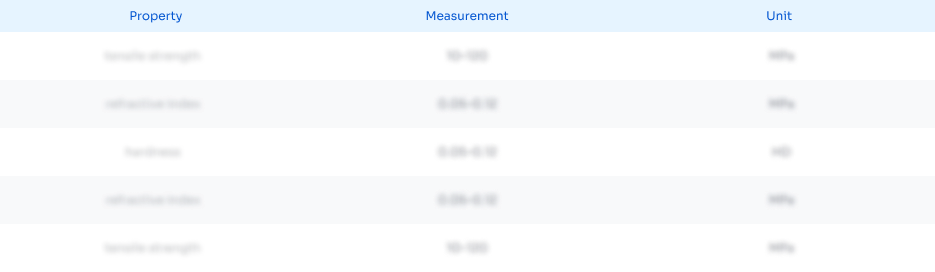
Abstract
Description
Claims
Application Information

- R&D
- Intellectual Property
- Life Sciences
- Materials
- Tech Scout
- Unparalleled Data Quality
- Higher Quality Content
- 60% Fewer Hallucinations
Browse by: Latest US Patents, China's latest patents, Technical Efficacy Thesaurus, Application Domain, Technology Topic, Popular Technical Reports.
© 2025 PatSnap. All rights reserved.Legal|Privacy policy|Modern Slavery Act Transparency Statement|Sitemap|About US| Contact US: help@patsnap.com