Composite fabric for making suitcases and bags and processing technology of composite fabric
A composite fabric and processing technology, applied in the field of light industry and textiles, can solve problems such as lack of grade, lack of three-dimensional effect, poor air permeability, etc., and achieve the effect of good work stability, simple structure, and improved quality
- Summary
- Abstract
- Description
- Claims
- Application Information
AI Technical Summary
Problems solved by technology
Method used
Image
Examples
Embodiment 1
[0070] like figure 1 As shown, the composite fabric for making the luggage includes the main body, and the main body is formed by laminating the PVC film 1 and the skeleton fabric layer 2 at a high temperature of 200°C. Wherein, the PVC film is prepared from the following raw materials in parts by weight: PVC resin 100; calcium carbonate 20; stabilizer 5; rutile titanium dioxide 3; plasticizer 45; soybean oil 2.5; The fabric of the skeleton fabric layer 2 is a polyester woven fabric with a fineness of 250D×250D and a density of 27×25 threads / inch.
[0071] To further illustrate, the thickness of the PVC film 1 is 18 filaments; the body is densely covered with through holes 22, the through holes 22 are straight holes and the extension direction of the axis is consistent with the distribution direction of the PVC film 1 and the skeleton fabric layer 2. In this embodiment, the diameter of the through hole 22 is preferably 0.6 mm. In the actual production of bags, a waterproof a...
Embodiment 2
[0104] The structure and principle of this embodiment two are basically the same as those of embodiment one, except that the PVC film is made of the following raw materials in parts by weight: PVC resin 100; calcium carbonate 25; stabilizer 5; rutile titanium dioxide 4; Plastic agent 45; soybean oil 2.5; color additive 2.75; the aperture of the through hole 22 is 1 mm.
[0105] The processing technology of the composite fabric for making bags includes a PVC film calendering process and a laminating process, and the PVC film calendering process is before the laminating process.
[0106] Wherein, the PVC film calendering process comprises the following steps:
[0107] A, metering: each raw material is weighed by weight;
[0108] B. Stirring and mixing: first pour the PVC resin into the mixer, then pour in the liquid raw materials, control the temperature at 105°C, stir at a speed of 350r / min, and stir for 180s; then pour in the powdery raw materials and control the temperature ...
Embodiment 3
[0122] The structure and principle of this embodiment three are basically the same as those of embodiment one, except that the PVC film is made of the following raw materials in parts by weight: PVC resin 100; calcium carbonate 30; stabilizer 5; rutile titanium dioxide 5; Plastic agent 45; soybean oil 2.5; color additive 3; the aperture of the through hole 22 is 1.8mm.
[0123] The processing technology of the composite fabric for making bags includes a PVC film calendering process and a laminating process, and the PVC film calendering process is before the laminating process.
[0124] Wherein, the PVC film calendering process comprises the following steps:
[0125] A, metering: each raw material is weighed by weight;
[0126] B. Stirring and mixing: first pour the PVC resin into the mixer, then pour in the liquid raw materials, control the temperature at 105°C, stir at a speed of 400r / min, and stir for 180s; then pour in the powdery raw materials and control the temperature ...
PUM
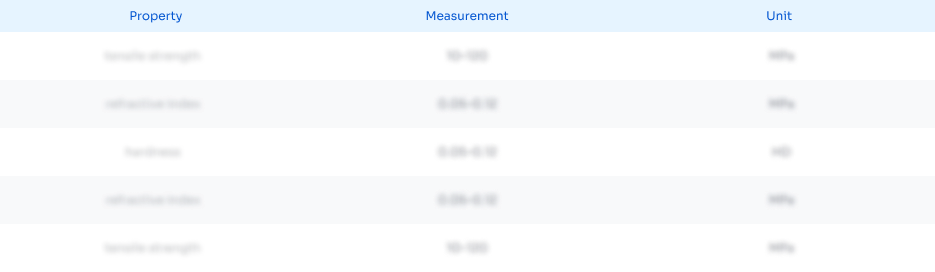
Abstract
Description
Claims
Application Information

- R&D
- Intellectual Property
- Life Sciences
- Materials
- Tech Scout
- Unparalleled Data Quality
- Higher Quality Content
- 60% Fewer Hallucinations
Browse by: Latest US Patents, China's latest patents, Technical Efficacy Thesaurus, Application Domain, Technology Topic, Popular Technical Reports.
© 2025 PatSnap. All rights reserved.Legal|Privacy policy|Modern Slavery Act Transparency Statement|Sitemap|About US| Contact US: help@patsnap.com