Phenolic foaming resin toughened with hydroxyl-terminated nitrile rubber
A technology for toughening hydroxy-terminated nitrile and rubber, which is applied in the field of phenolic foamed resin toughened by hydroxy-terminated nitrile rubber, can solve the problems of poor stability of phenolic resin, inability to achieve homogeneous blending, and uneven rubber distribution. To achieve the effect of short reaction cycle, appropriate hardness and reduced embrittlement
- Summary
- Abstract
- Description
- Claims
- Application Information
AI Technical Summary
Problems solved by technology
Method used
Examples
Embodiment 1
[0027] The present invention is a kind of toughened phenolic resin of hydroxy-terminated nitrile rubber, comprising the following steps:
[0028] Set the temperature of the water bath at about 60°C, add 65g of phenol solution into a three-necked flask equipped with a stirring paddle, then add 0.65g of sodium hydroxide and stir evenly for about 5 minutes, and react for half an hour to activate the phenol and separate Add 35g of paraformaldehyde in batches, control the temperature at 60°C within half an hour, keep warm for half an hour after adding all the paraformaldehyde to fully react, then add 5.2g of hydroxy-terminated nitrile rubber, stir magnetically for 10 minutes, and pass N2 protection , slowly raise the temperature to 90°C at a heating rate of 3°C / min, react at constant temperature for about one and a half hours, cool down to 75°C, adjust the pH to 7-8 with acetic acid, dehydrate, and cool the synthesized phenolic resin for 24 hours to obtain modification The target p...
Embodiment 2
[0030] The present invention is a kind of toughened phenolic resin of hydroxy-terminated nitrile rubber, comprising the following steps:
[0031] Set the temperature of the water bath at about 60°C, add 65g of phenol solution into a three-necked flask equipped with a stirring paddle, then add 0.65g of sodium hydroxide and stir evenly for about 5 minutes, and react for half an hour to activate the phenol and separate Add 35g of paraformaldehyde in batches, control the temperature at 60°C within half an hour, keep warm for half an hour to fully react the paraformaldehyde, then add 6.5g of hydroxy-terminated nitrile rubber, stir magnetically for 10 minutes, and pass N2 protection , slowly raise the temperature to 90°C at a heating rate of 3°C / min, react at constant temperature for about one and a half hours, cool down to 75°C, adjust the pH to 7-8 with acetic acid, dehydrate, and cool the synthesized phenolic resin for 24 hours to obtain modification The target phenolic resin.
Embodiment 3
[0033] The present invention is a kind of toughened phenolic resin of hydroxy-terminated nitrile rubber, comprising the following steps:
[0034] Set the temperature of the water bath at about 60°C, add 65g of phenol solution into a three-necked flask equipped with a stirring paddle, then add 0.65g of sodium hydroxide and stir evenly for about 5 minutes, and react for half an hour to activate the phenol and separate Add 35g of paraformaldehyde in batches, control the temperature at 60°C within half an hour, keep warm for half an hour to fully react the paraformaldehyde, then add 9.75g of hydroxy-terminated nitrile rubber, stir magnetically for 10 minutes, and pass N2 protection , slowly raise the temperature to 90°C at a heating rate of 3°C / min, react at constant temperature for about one and a half hours, cool down to 75°C, adjust the pH to 7-8 with acetic acid, dehydrate, and cool the synthesized phenolic resin for 24 hours to obtain modification The target phenolic resin. ...
PUM
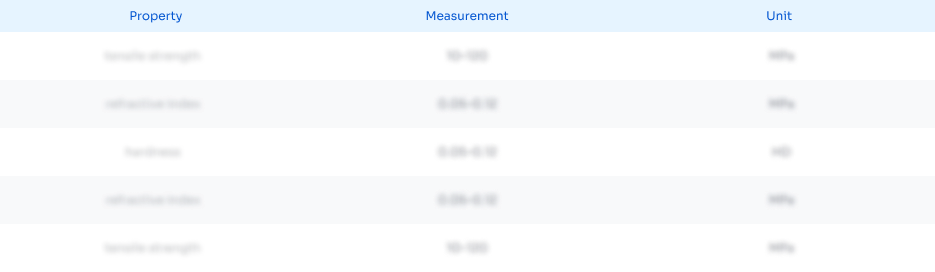
Abstract
Description
Claims
Application Information

- R&D Engineer
- R&D Manager
- IP Professional
- Industry Leading Data Capabilities
- Powerful AI technology
- Patent DNA Extraction
Browse by: Latest US Patents, China's latest patents, Technical Efficacy Thesaurus, Application Domain, Technology Topic, Popular Technical Reports.
© 2024 PatSnap. All rights reserved.Legal|Privacy policy|Modern Slavery Act Transparency Statement|Sitemap|About US| Contact US: help@patsnap.com