Ceramic material for grinding head
A ceramic material and grinding head technology, which is applied in the field of ceramic grinding head material composition, can solve the problems of reducing production costs and achieve the effect of fine surface
- Summary
- Abstract
- Description
- Claims
- Application Information
AI Technical Summary
Problems solved by technology
Method used
Examples
Embodiment 1
[0031] In this embodiment, the material of the outer grinding head is composed of 82.5% of aluminum oxide, 8% of magnesium oxide, 6% of silicon oxide and 3.5% of titanium dioxide with a purity of ≥99%; the material of the inner grinding head is composed of 52% of alumina with purity ≥99%, 20% of zirconia with purity ≥94%, 7% of magnesium oxide, 8% of silicon oxide and 14% of titanium dioxide. The molding pressure used is 430MPa for the outer grinding head and 450MPa for the inner grinding head; the initial firing temperature is 700°C-800°C for the outer grinding head and 550°C-600°C for the inner grinding head; Then the final firing is carried out in two stages. The two stages here mean that the temperature rise process is carried out in two stages, and the final refining temperature is 1675°C-1685°C; the refining uses a hydrogen furnace. This embodiment is the optimal technical solution.
Embodiment 2
[0033] In this embodiment and subsequent embodiments, only the composition of each material and the molding pressure are changed, and the rest are the same as in Embodiment 1.
[0034]The material of the outer grinding head is composed of 80% of alumina, 12% of magnesium oxide, 5% of silicon oxide and 3% of titanium dioxide with a purity of ≥99%; the material of the inner grinding head is composed of 80% of purity ≥99% by weight. 50% of aluminum oxide, 25% of zirconia with purity ≥94%, 5% of magnesium oxide, 5% of silicon oxide and 15% of titanium dioxide. The molding pressure adopted is that the molding pressure of the outer grinding head is 410MPa, and the molding pressure of the inner grinding head is 430MPa.
Embodiment 3
[0036] The material of the outer grinding head is composed of 85% of alumina, 6% of magnesium oxide, 5% of silicon oxide and 4% of titanium dioxide with a purity of ≥99%; the material of the inner grinding head is composed of 85% of purity ≥99% by weight. 55% of aluminum oxide, 27% of zirconia with purity ≥94%, 3% of magnesium oxide, 3% of silicon oxide and 12%. The molding pressure adopted is that the molding pressure of the outer grinding head is 420MPa, and the molding pressure of the inner grinding head is 440MPa.
PUM
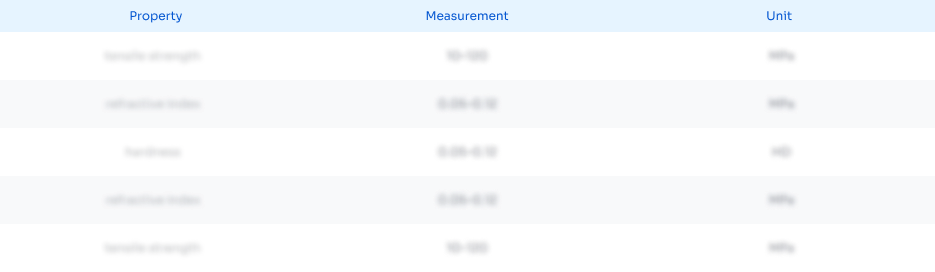
Abstract
Description
Claims
Application Information

- Generate Ideas
- Intellectual Property
- Life Sciences
- Materials
- Tech Scout
- Unparalleled Data Quality
- Higher Quality Content
- 60% Fewer Hallucinations
Browse by: Latest US Patents, China's latest patents, Technical Efficacy Thesaurus, Application Domain, Technology Topic, Popular Technical Reports.
© 2025 PatSnap. All rights reserved.Legal|Privacy policy|Modern Slavery Act Transparency Statement|Sitemap|About US| Contact US: help@patsnap.com