A kind of steel slag aluminothermic reduction method for producing ferroalloy and refining slag
A ferroalloy and refining slag technology, applied in the field of comprehensive utilization of metallurgical slag, can solve the problems of low added value of products and low recovery rate of steel slag resources, and achieve the effects of high added value of products, high resource utilization efficiency, and simple operation
- Summary
- Abstract
- Description
- Claims
- Application Information
AI Technical Summary
Problems solved by technology
Method used
Examples
Embodiment 1
[0042]The mass percentages of the main chemical components of liquid steel slag are: MFe 4.38%, FeO 15.46%, Fe 2 o 3 9.65%, SiO 2 10.63%, CaO 46.95%, MgO 4.96%, Al 2 o 3 3.64%, MnO 2.48%, P 2 o 5 1.85%. .
[0043] The process steps are as follows: put 100kg of liquid steel slag and 7.8kg of metallic aluminum into the first reactor, that is, the steel slag ladle, and carry out preliminary reduction by electromagnetic stirring for 10 minutes to prepare phosphorus-containing molten iron. The phosphorus-containing molten iron settles at the bottom of the steel slag ladle, and the molten iron The upper layer is slag; after the initial reduction is completed, pour the upper layer of slag into the second reactor, that is, the steel slag ladle, add 7kg of metal aluminum and carry out the second step of reduction by electromagnetic stirring for 10 minutes to prepare silicon-manganese alloy, and the obtained silicon-manganese alloy It settles to the bottom of the ladle, and the...
Embodiment 2
[0046] The mass percentages of the main chemical components of liquid steel slag are: MFe 3.45%, FeO 11.51%, Fe 2 o 3 17.90%, SiO 2 13.08%, CaO 42.50%, MgO 4.38%, Al 2 o 3 4.66%, MnO 1.29%, P 2 o 5 1.23%.
[0047] The process steps are as follows: put 100kg of liquid steel slag and 9.7kg of metallic aluminum into the first reactor, that is, the molten iron ladle, and carry out preliminary reduction by mechanical stirring for 60 minutes to prepare phosphorus-containing molten iron. The phosphorus-containing molten iron settles at the bottom of the ladle, and the molten iron The upper layer is molten slag; after the initial reduction is completed, the molten slag is poured into the second reactor, that is, the ladle, and 8.2kg of metallic aluminum is added to carry out the second step of reduction by electromagnetic stirring for 40 minutes to prepare silicon-manganese alloy, and the obtained silicon-manganese alloy It settles to the bottom of the ladle, and the slag is o...
Embodiment 3
[0050] The mass percentages of the main chemical components of liquid steel slag are: MFe 1.34%, FeO 12.86%, Fe 2 o 3 13.18%, SiO 2 11.11%, CaO 44.33%, MgO 7.82%, Al 2 o 3 4.54%, MnO 2.67%, P 2 o 5 2.15%.
[0051] The process steps are as follows: put 100kg of liquid steel slag and 8.8kg of metallic aluminum into the first reactor, that is, the ladle, and conduct preliminary reduction by electromagnetic stirring for 60 minutes to prepare phosphorus-containing molten iron, which settles at the bottom of the ladle. The upper layer of molten iron is molten slag; after the initial reduction is completed, the molten slag is poured into the second reactor, that is, the steel slag ladle, and 7.3kg of metal aluminum is added to carry out the second step of reduction by electromagnetic stirring for 60 minutes to prepare silicon-manganese alloy, and the obtained silicon-manganese The alloy settles to the bottom of the steel slag ladle, and the slag is on the upper layer; the upp...
PUM
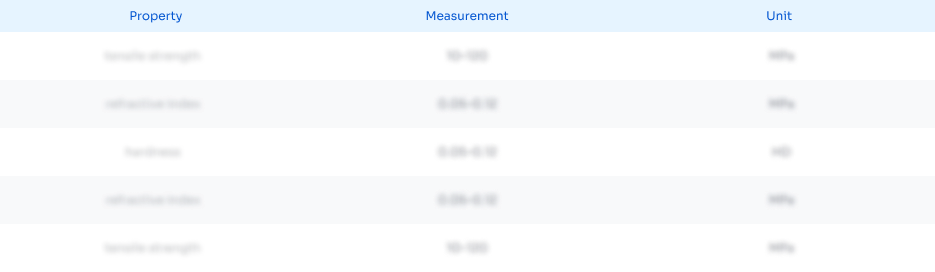
Abstract
Description
Claims
Application Information

- R&D
- Intellectual Property
- Life Sciences
- Materials
- Tech Scout
- Unparalleled Data Quality
- Higher Quality Content
- 60% Fewer Hallucinations
Browse by: Latest US Patents, China's latest patents, Technical Efficacy Thesaurus, Application Domain, Technology Topic, Popular Technical Reports.
© 2025 PatSnap. All rights reserved.Legal|Privacy policy|Modern Slavery Act Transparency Statement|Sitemap|About US| Contact US: help@patsnap.com