Self-adaptive direct slicing method for preparing biological scaffold
A bio-scaffold, self-adaptive technology, applied in the application, image generation, manufacturing auxiliary devices, etc., can solve the problem of no biological scaffold structural characteristic characterization parameters, etc., to avoid repeated sectioning, avoid complex and time-consuming, and enhance robustness. Effect
- Summary
- Abstract
- Description
- Claims
- Application Information
AI Technical Summary
Problems solved by technology
Method used
Image
Examples
Embodiment
[0049] Such as figure 1 As shown, the present invention is mainly divided into four parts, ① preprocessing, ② thickness adaptive processing (ESD and IAD), ③ direct slicing and ④ postprocessing. The ESD sub-step and the IAD sub-step of the two components of the thickness adaptive processing are two completely independent steps, and there is no overlap of operands and operands.
[0050] The thickness adaptive processing ② is directly independent of the direct slicing step. The direct slicing step can accept the data processed by the thickness adaptive processing step to perform the thickness adaptive direct slicing operation, or skip the thickness adaptive processing step and directly accept the preprocessing step. The processed data was subjected to a uniform thickness direct slicing operation. These four steps constitute a dialog-based application with human-computer interaction in its user interface. The inheritance relationship of this dialog class is "class Slicer_Dlg: pu...
PUM
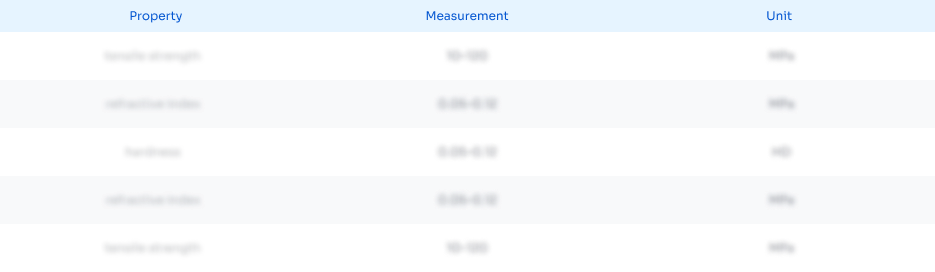
Abstract
Description
Claims
Application Information

- R&D
- Intellectual Property
- Life Sciences
- Materials
- Tech Scout
- Unparalleled Data Quality
- Higher Quality Content
- 60% Fewer Hallucinations
Browse by: Latest US Patents, China's latest patents, Technical Efficacy Thesaurus, Application Domain, Technology Topic, Popular Technical Reports.
© 2025 PatSnap. All rights reserved.Legal|Privacy policy|Modern Slavery Act Transparency Statement|Sitemap|About US| Contact US: help@patsnap.com