Cuprous modified zeolite diesel engine emission pollutant oxidation and purification catalyst
A technology for purifying catalysts and molecular sieves, applied in physical/chemical process catalysts, organic compounds/hydrides/coordination complex catalysts, mechanical equipment, etc., can solve difficult problems such as improving catalytic activity, reducing production costs, Effect of improving sulfur resistance and heat deactivation performance
- Summary
- Abstract
- Description
- Claims
- Application Information
AI Technical Summary
Problems solved by technology
Method used
Image
Examples
preparation example Construction
[0043] (3) Preparation of coating slurry
[0044] The prepared monovalent copper-modified ZSM-5 molecular sieve and La(NO 3 ) 3 ·6H 2 O, Ce(NO 3 ) 3 ·6H 2 O, Zr(NO 3 ) 4 ·5H 2 O, pure γ-Al 2 o 3 Powder, pure TiO 2 The powder, aluminum sol, silica sol, polyethylene glycol, and nitric acid are added to deionized water whose total mass is 10 to 15 times that of the catalytic coating, and fully stirred to form a uniform slurry. The pH value of the homogeneous slurry is adjusted to 3-4 with 1 mol / L sodium hydroxide solution or glacial acetic acid. The uniform slurry is ground on a wet grinder until the D50 particle size is in the range of 1.0-1.2 μm, and then the ground uniform slurry is stirred at 60-80° C. for 16-24 hours to obtain the coating slurry.
[0045] (4) Coating of coating slurry
[0046] Design the mass of the 400-mesh cordierite honeycomb ceramic carrier to be coated with the catalytic coating; weigh the cylindrical 400-mesh cordierite honeycomb ceramic c...
Embodiment 1
[0049] (1) Determination of the amount of preparation and supported catalyst raw materials
[0050] In the main catalyst of the catalyst prepared in Design Example 1, monovalent copper modified ZSM-5 molecular sieve and La 2 o 3 The mass percentage is: 60%:40%; Cu in monovalent copper modified ZSM-5 molecular sieve 2 The mass percent of O and ZSM-5 molecular sieve is: 10%: 90%; CeO in cocatalyst 2 and ZrO 2The mass percentage is: 60% / 40%. The mass percent of main catalyst, co-catalyst and coating base material is: 20%:20%:60%. Among coating base materials, SiO 2 、TiO 2 with γ-Al 2 o 3 The mass percentage is: 20%:20%:60%, of which all γ-Al 2 o 3 Medium pure γ-Al 2 o 3 γ-Al produced by calcination of powder and aluminum sol 2 o 3 The mass percentage is: 75%: 25%. Every 100g of catalytic coating requires 10g of polyethylene glycol with an average molecular weight of 20,000 and 50g of nitric acid; every 100g of monovalent copper-modified ZSM-5 molecular sieve requir...
Embodiment 2
[0059] (1) Determination of the amount of preparation and supported catalyst raw materials
[0060] In the main catalyst of the catalyst prepared in Design Example 2, monovalent copper modified ZSM-5 molecular sieve and La 2 o 3 The mass percentage is: 80%:20%; Cu in monovalent copper modified ZSM-5 molecular sieve 2 The mass percent of O and ZSM-5 molecular sieve is: 13%: 87%; CeO in cocatalyst 2 and ZrO 2 The mass percentage is: 60% / 40%. The mass percent of main catalyst, co-catalyst and coating base material is: 10%:15%:75%. Among coating base materials, SiO 2 、TiO 2 with γ-Al 2 o 3 The mass percentage is: 20%:30%:50%, where γ-Al 2 o 3 Medium pure γ-Al 2 o 3 γ-Al produced by calcining powder and aluminum sol 2 o 3 The mass ratio is: 75%:25%. Every 100g of catalytic coating requires 15g of polyethylene glycol with an average molecular weight of 20,000 and 25g of nitric acid; every 100g of monovalent copper-modified ZSM-5 molecular sieve corresponds to 300ml of...
PUM
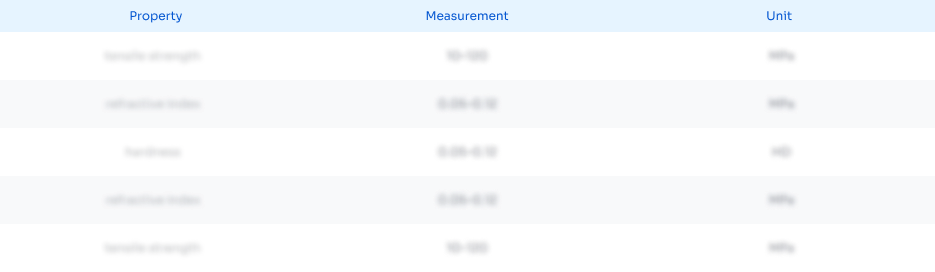
Abstract
Description
Claims
Application Information

- R&D
- Intellectual Property
- Life Sciences
- Materials
- Tech Scout
- Unparalleled Data Quality
- Higher Quality Content
- 60% Fewer Hallucinations
Browse by: Latest US Patents, China's latest patents, Technical Efficacy Thesaurus, Application Domain, Technology Topic, Popular Technical Reports.
© 2025 PatSnap. All rights reserved.Legal|Privacy policy|Modern Slavery Act Transparency Statement|Sitemap|About US| Contact US: help@patsnap.com